History
"We deliver world class performance" our philosophy hasn't changed since we were founded in 1914.
We would like to share our journey with you.
- Group photo at the Isa cement plant under construction with a master engineer from Loesche of West Germany, 1955 -
- Milestones of UBE Machinery
- Chronology
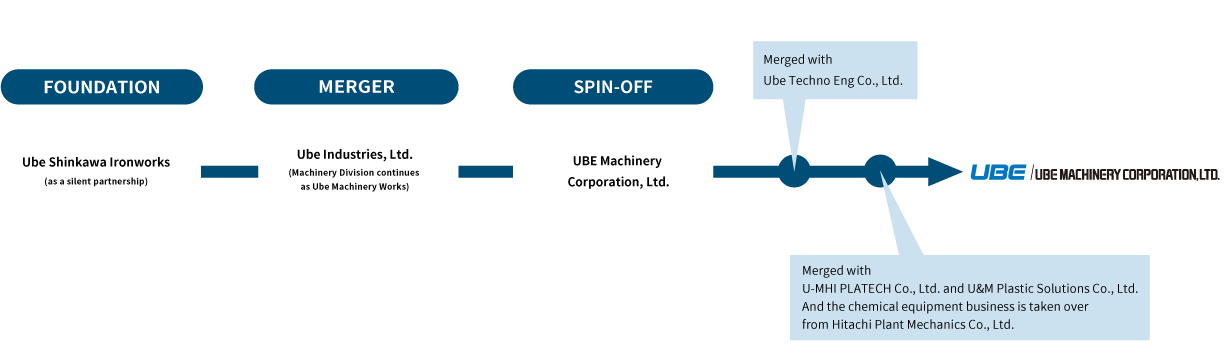
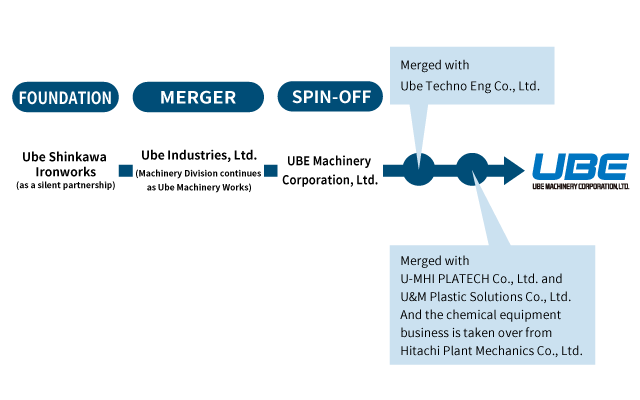
- References
- Ube Industries ,Ltd.1998.Ube Kosan sogyo hyaku-nen shi. Japan
- Ube Industries ,Ltd.2019.Ube Kosan 120-nen shi. Japan
- UBE Machinery Co. ,Ltd.2009.Ube Kosankikai 10-nen no ayumi. Japan
1914 - 1945
The Origin of UBE Machinery
- Coexistence & Mutual Prosperity, Finite Mining to Infinite Industry -
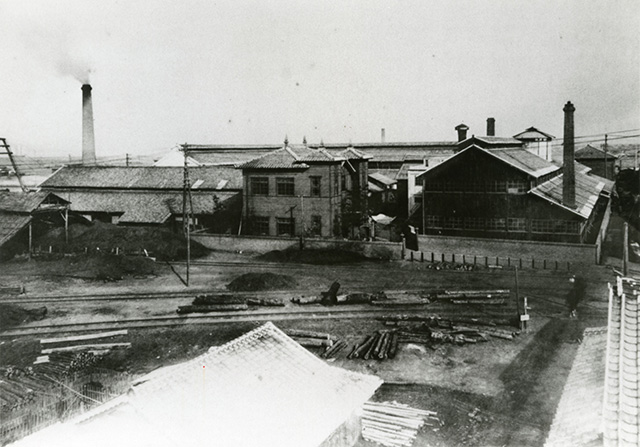
In 1914, Ube Shinkawa Ironworks, the origin of our company, was established.
Based on the spirit of its founding, the company expanded its business from coal mining machinery to kilns and other plant equipment, laying the foundation for today's industrial machinery business. In 1942, during the wartime control economy, Ube Industries, Ltd. was established through the merger of the Okinoyama Coal Mine and four related companies in the machinery, cement, and chemical industries.
1914
"Ube Shinkawa Ironworks(now UBE Machinery Co.,Ltd.)" WAS ESTABLISHED AS A SILENT PARTNERSHIP
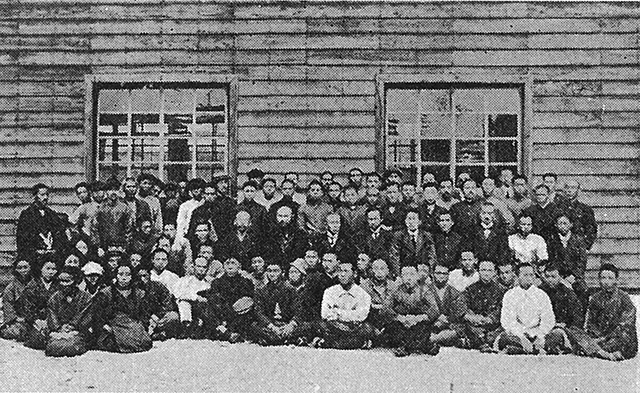
On January 15, 1914, Ube Shinkawa Ironworks was born with about 70 employees and 100,000 yen in capital.
The company started with a one-story wooden factory consisting of four buildings: one each for lathe, finishing, casting, can manufacturing, forging, and boiler.
The company's main products in its early years were coal mining machinery, including winders, coal wagons, pumps, and crushers.
In 1917, four years after its founding, the company was reorganized as Ube Ironworks Co.
1924
Supplied peripheral equipment for Ube Cement's giant kiln. This will lead to in-house production in the future.
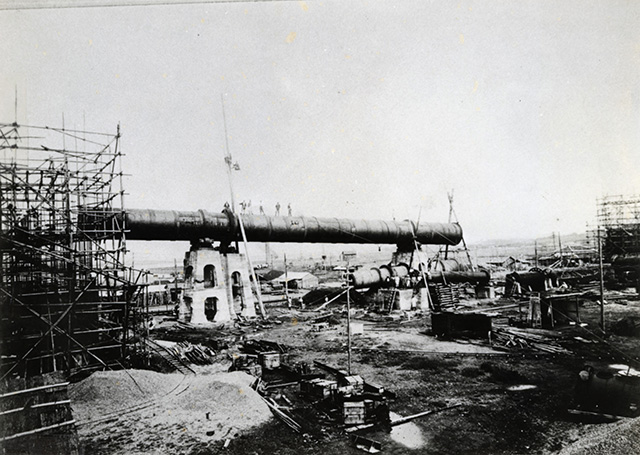
In 1924, at Ube Cement Manufacturing, which had been established the previous year, a huge kiln (*) with a diameter of 3 meters and a length of 50 meters.
The people at that time were talking about "how a huge cannon was installed toward Kyushu".
Ube Ironworks was involved in the manufacture of key devices for the kiln, including the undercooler.
(*) A kiln is used for firing cement, insulators, ceramics, etc.
PRODUCTS_Kiln & Dryer1942
"RISE IN MINING, UNITE IN INDUSTRY" - Ube Industries, Ltd. Was Established -
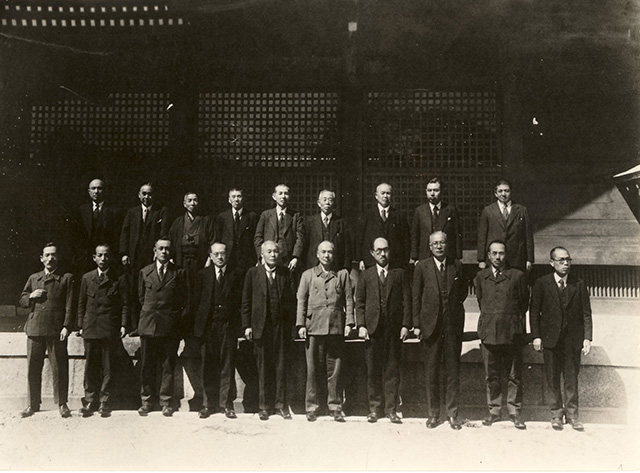
After the inauguration of the Okinoyama Coal Mine in 1897, Ube Ironworks, a mining machinery company, Ube Cement Manufacturing, which uses Ube coal and its waste soil, and Ube Nitrogen Industry, which uses Ube coal as fuel and raw materials, were successively established.
These companies developed based on Ube's human resources and capital, and were conscious of the prosperity of the region.
On March 10, 1942, under the tightening of the war situation and the severer control economy, these four companies, which also had Ube's coal as a background, merged to establish Ube Industries, Ltd.
Ube Machinery Works was established as one of the plants of Ube Industries.
1946 - 1972
Pioneering New Innovations
- Modernization of Ube Machinery Works During Postwar Reconstruction & High Economic Growth -
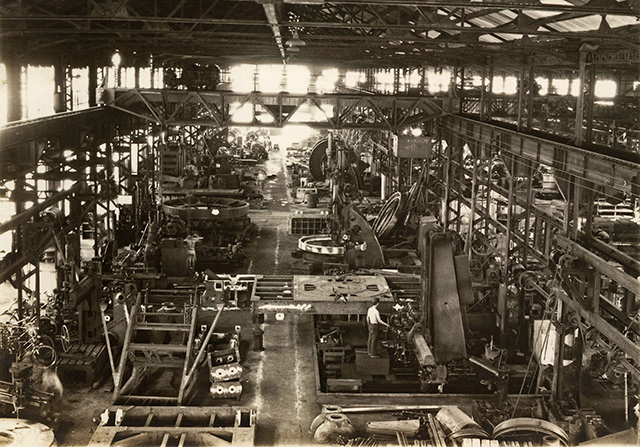
After recovering from the postwar chaos, Japanese industry underwent a period of great change and achieved rapid economic growth.
Ube Industries' machinery business: Ube Machinery Works, also struggled to survive, introducing advanced Western technology and promoting independent technological development, and pioneered new core businesses such as molding machines.
In 1972, the production base relocated to Okinoyama, and built a group of plants equipped with state-of-the-art facilities and established the current production system of Ube's main plant.
1953
"Screening Equipment" NO. 1 DEVELOPED
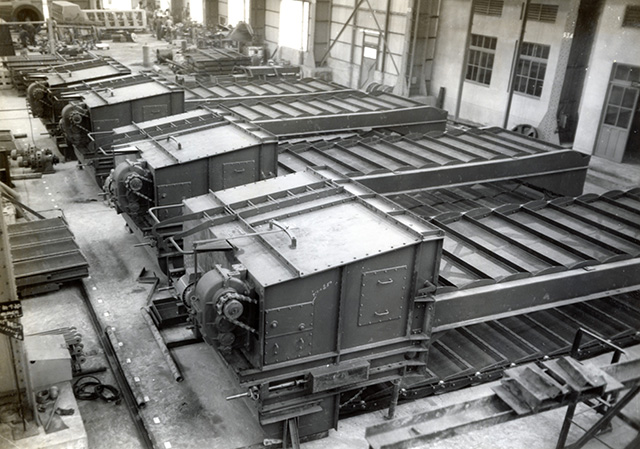
In the process of seeking new opportunities for machinery products after the war, there were several areas that were strategically developed.
One of them was to enter the electric power industry, with which we had a relationship through its coal-related machinery business.
With postwar reconstruction underway, we began supplying screen equipment to thermal power plants, which were in the midst of a construction boom due to increased demand for electricity. This equipment removed jellyfish and dust from seawater used to cool generators, contributing greatly to the stable supply of electric power.
We have been manufacturing this equipment since its pioneering period, and have established an unshakeable position in this field up to the present day.
1958
"Vertical Mill" NO. 1 DEVELOPED
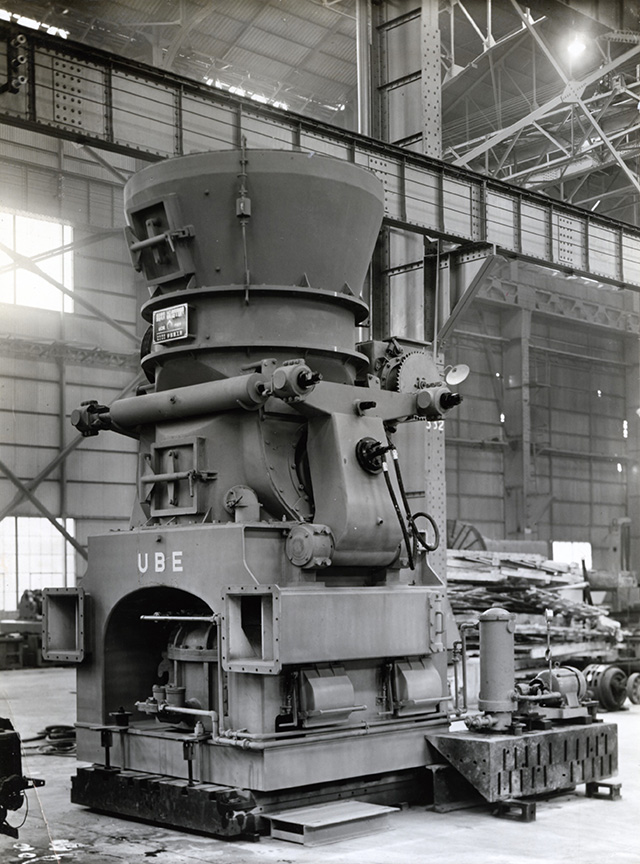
The first result of a business tour to Europe and the U.S. was a technical tie-up with LOESCHE AG of West Germany for mills, shaft-kilns, and pelletizers. The vertical mill* manufactured by us in the cooperation had many advantages over conventional tube mills, such as compactness, low noise, and low cost, and gradually gained recognition for its performance.
While we lost its mainstay products due to the change in energy structure from coal to oil and suffered from slow growth in new orders, new businesses such as vertical mills, limestone calcination furnaces, and diesel engines, which were launched through aggressive technical cooperation with European, American, and Japanese companies, contributed greatly to the modernization of Ube Machinery Works.
(*) A vertical mill is a device that crushes cement materials and coal by crushing and grinding them between a rotating table and rollers.
1960
ENTRY INTO THE DIE CASTING MACHINE BUSINESS & THE EXTRUSION PRESS BUSINESS
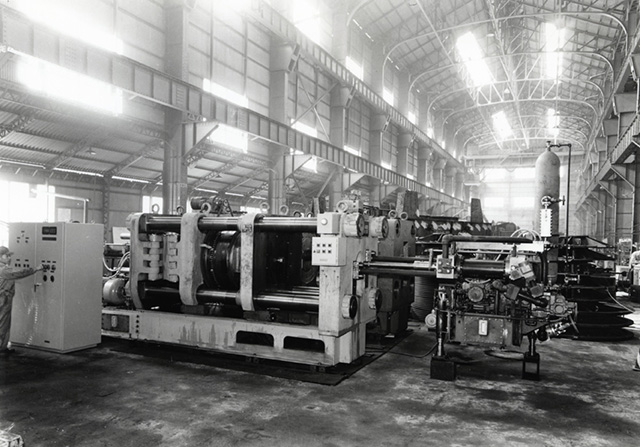
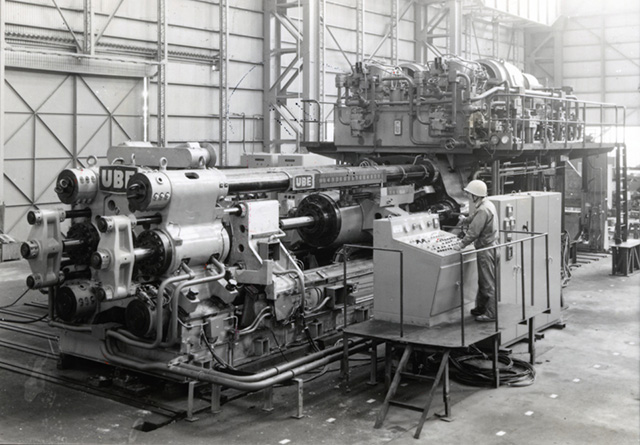
The impetus for entering the die casting machine business and the extrusion press business, which are now our flagship products, came from an awareness of issues related to Japan's industry as a whole.
In the 1950s, the ratio of die press machines to the number of machine tools owned in Japan was less than half that of the United States.
Due to the lack of die press machines, the production of machine parts often relied on machine tools, which required a large number of cutting processes, leading to high product costs. In addition, domestic presses, of which there were about 100 manufacturers, were all small in size, and large, high-performance die press machines had to be imported from overseas.
Predicting the growth in demand for aluminum products, a component of the housing and automobile industries, which were expected to develop rapidly, we focused on die-casting machines and extrusion presses and established into a technical alliance with Lake Erie Machinery, Inc. of the U.S. to design its own presses.
However, of the seven project members, three were new hires, and the average age was 23. They were new to everything, let alone presses, but they were eager to learn.
Despite various troubles, they succeeded in the development and delivered the first die casting machine in 1962 and the first extrusion press in 1964.
1966
"Biedenbach kiln" DEBUT - Improvement in quality of quicklime -
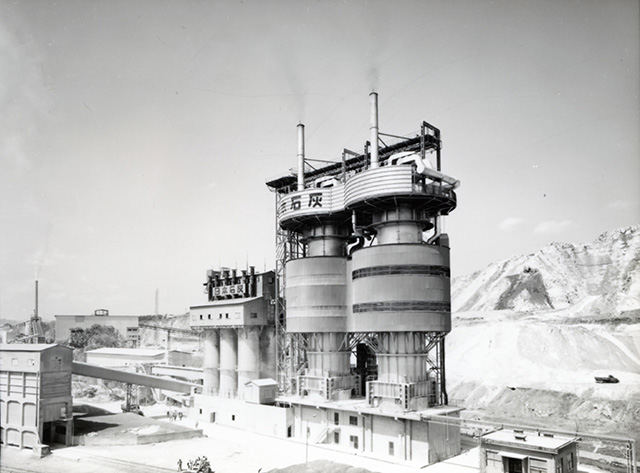
Japan was in the midst of a period of rapid economic growth, and demand for quicklime, which is used in cement, steelmaking, and other industries, was rapidly increasing.
Ube Machinery Works, which had a number of quicklime manufacturers and users among its affiliated companies, was in desperate need of a calcination kiln that could increase the purity of the quicklime and ensure stable production.
Against this backdrop, in 1966, Ube Machinery Works completed and delivered its first Beckenbach kiln (limestone calcination furnace) through a technical tie-up with the West German company.
The kiln improved the quality of quicklime and significantly reduced production costs, and it was greatly welcomed by users of quicklime supplies.
1967
ENTRY INTO THE INJECTION MOLDING MACHINE BUSINESS
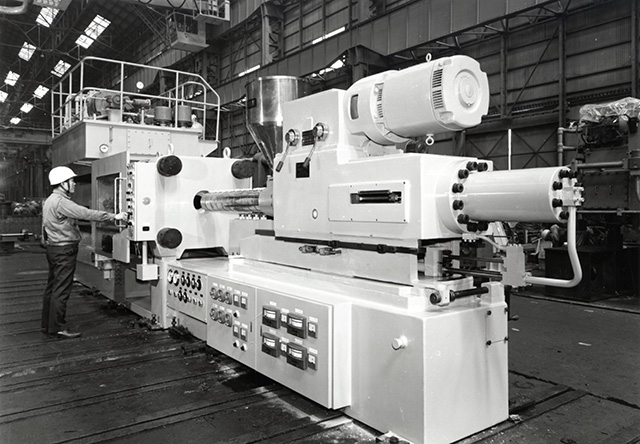
As the world entered the plastic age during the heyday of home appliances, and our die casting machine business was getting on track, we decided to enter the injection molding machine industry, which had a much larger market, because the die clamping device could be shared with die casting machines, and as a plastic manufacturer, we could sell plastic along with the machines.
In March 1967, an injection molding machine with screw-in-line system was developed in-house, and in September of the same year, an injection molding machine was launched through a technical tie-up with BorgWarner Inc. of the U.S.
With ABS resin developed by the Chemical Division, we began sales of injection molding machines and received orders from the domestic automobile industry and other customers.
1972
MOVED THE BASE OF OPERATIONS TO OKINOYAMA - The beginning of a production system that continues to the present day -
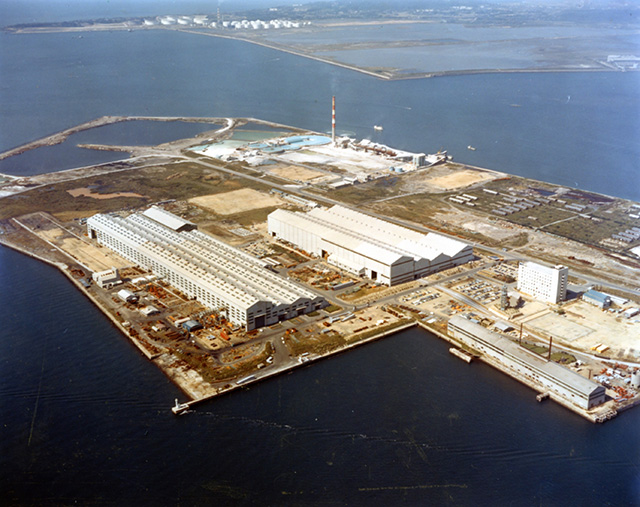
As the high economic growth progressed, the trend toward larger models manufactured by Ube Machinery Works was further accelerated.
However, the production capacity of the existing plant had already reached its limit. In 1968, the decision was made to relocate and build a new plant on a large site that included the former site of the closed Okinoyama Coal Mine and its adjacent land. The new plant was completed in 1972, after a thorough pursuit of the best layout for the most rational process sequence from processing of materials and parts, assembly, to shipping.
Thus, over a period of five years and at a total cost of 8.7 billion yen, Ube Machinery Works was transformed into a group of plants equipped with large, high-performance, state-of-the-art facilities.
1973 - 1999
Meeting Diversifying Demands
- Focusing on high-value-added & environmentally friendly products -
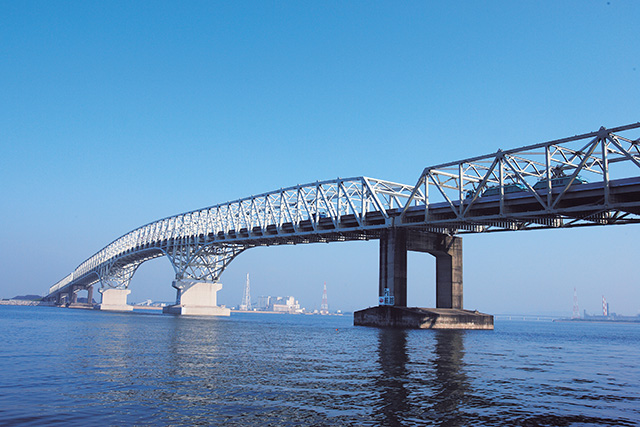
In 1973, the First Oil Crisis hit the world.
Confronted with growing energy conservation awareness and diversifying user demands, we boldly took on the challenge of developing world and industry-first technologies.
In order to expand its scale, we entered the U.S. market early, at a time when the Big Three automobile industry was thriving, and built the foundation of our North American business.
During this period, we also began the bridge business, which has led to today's product lineup.
1976
WORLD’S FIRST FULLY AUTOMATIC NO-BURR DIE CASTING MACHINE "UNI-FF" NO.1 WENT ON SALE - Breakthrough in the die casting machine business -
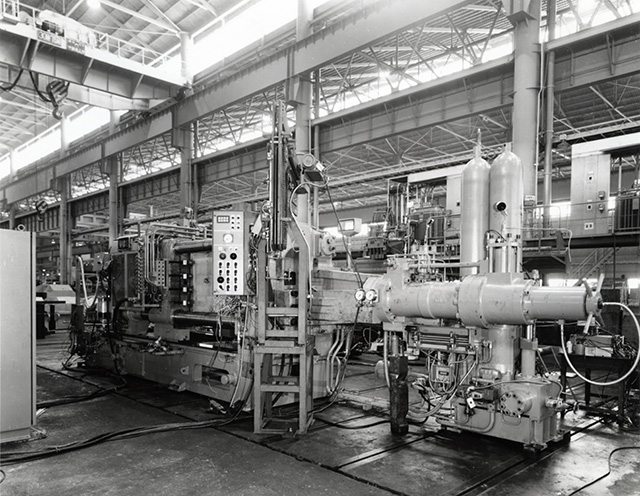
Since the delivery of the initial die casting machine in 1962, larger and larger machines have been produced.
However, after the oil crisis, the automobile industry, which was the main user of die casting machines, became even more fuel-efficient, and aluminum parts were increasingly used to reduce the weight of car bodies.
We anticipated this trend from an early stage and aimed to develop a no-burr die casting machine.
Without burrs, the finishing process can be simplified and the die casting machine can be operated unmanned in the casting process, resulting in significant labor savings.
As a result of trial and error, we succeeded in developing the world's first fully automatic no-burr die casting machine "UNI-FF," which incorporates a computer in all processes from aluminum casting to product removal from the mold.
Then, our UNI-FF received orders from major Japanese automakers, and we expanded our supply to the Big Three automakers as well as other automakers in Europe and the U.S.
SELF-DEVELOPED "UBEMAX injection molding machine" NO. 1 WENT ON SALE - Increased orders for injection molding machines -
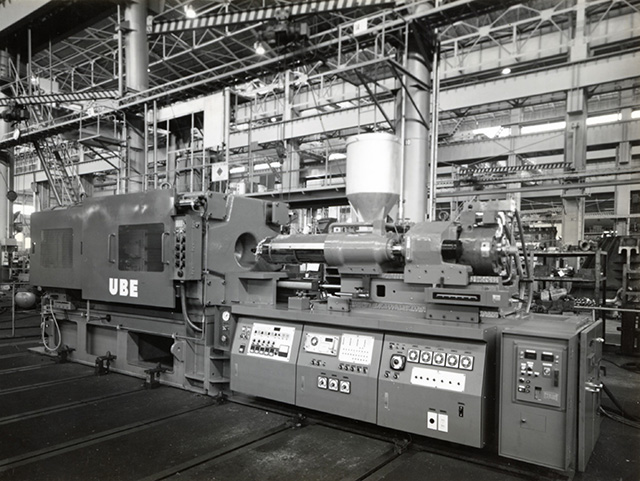
In the business of injection molding machines, in 1976, we launched its proprietary "UBEMAX injection molding machine," which incorporated an in-line screw system.
This machine is equipped with a high-cycle toggle mechanism in the mold clamping unit and achieves overwhelming energy savings compared to conventional machines.
Similar to our die casting machines, sales of injection molding machines grew as a result of the increased use of plastics for the purpose of reducing the weight of automobiles.
We produced the world's largest toggle-type injection molding machine at the time, with a clamping force of 2500 metric tons, and later, more than 3000 metric tons, and supplied the machine to almost all automobile manufacturers in the world.
Not satisfied with the delivery of the machine, we made continuous efforts to improve the quality of the machine, and this sincere attitude led to the receipt of a very large order in the U.S. years later.
1978
DEVELOPMENT OF INDUSTRIAL MACHINERY PRODUCTS
- Adapted to the era of high value-added products -
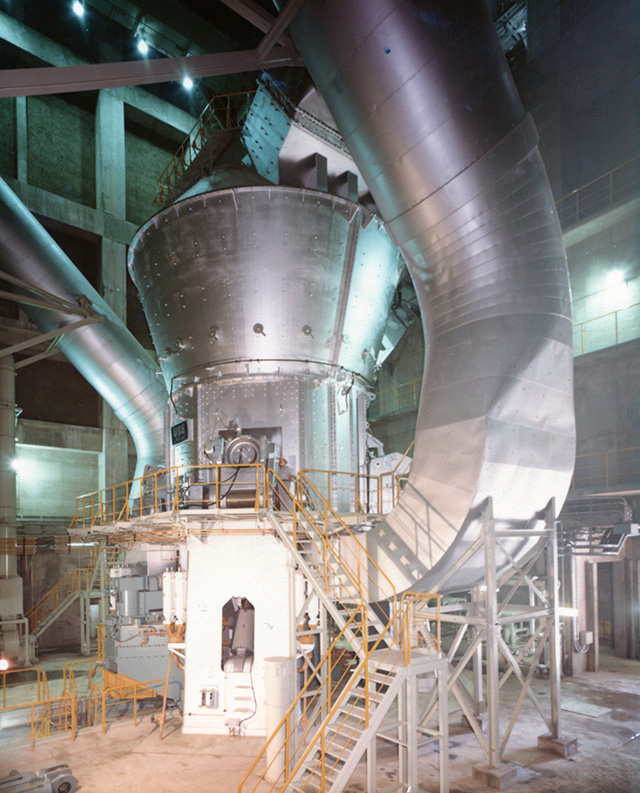
In order to respond to the changing times of energy conservation, our industrial machinery business products have promoted the improvement of existing models as well as the incorporation of new technologies. As a result, each model of industrial machinery, such as cement manufacturing machinery, achieved both scale effects and energy savings.
In the business of mill equipment, the "UBE-LOESCHE Mill LM/42" was developed to realize the "one kiln, one mill" method, which greatly contributes to reducing equipment and running costs in cement production, and boasted a production capacity of 550 tons per hour, the largest in the world at the time.
1982
PIONEERING DEVELOPMENT OF THE BRIDGE BUSINESS: Opening of the Kosan Ohashi Bridge
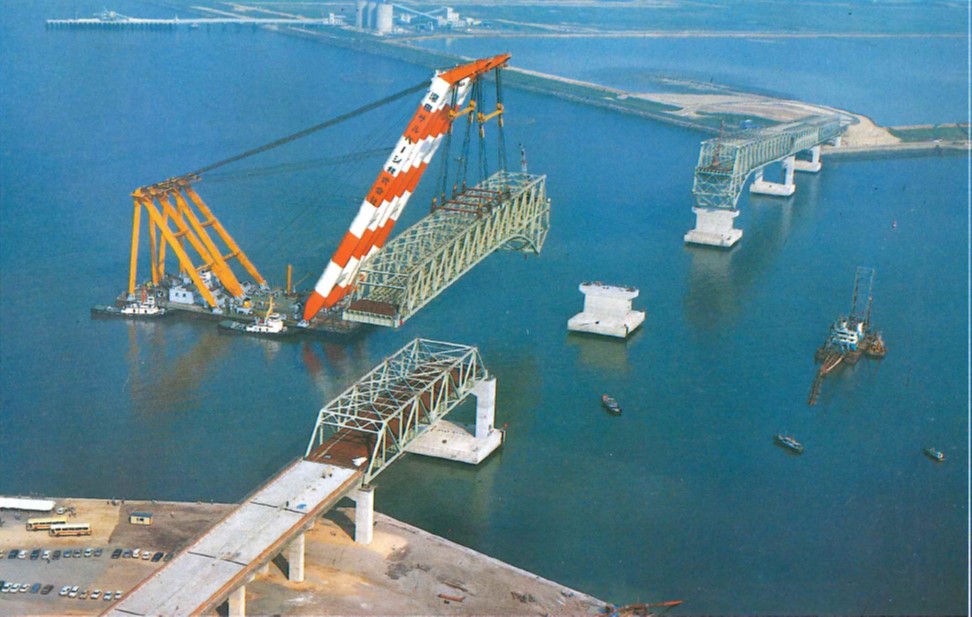
After the oil crisis, Ube Industries worked hard to add value to its products, especially in the energy conservation efforts.
At the same time, we planned to construct the Kosan Ohashi Bridge, a large-scale bridge that would be the culmination of the Ube Industries private road (a dedicated automobile road between Isa and Ube) for the development of the entire Ube region.
This bridge was to be built at the mouth of the 800-meter wide river between Okinoyama and Nishi Okinoyama, and had to be strong enough to support four 100-ton ultra-large double trailers traveling simultaneously, with bridge girders high enough to accommodate 20,000-ton ships, and completed in two-and-a-half years.
After careful consideration, the bridge design team decided to erect the truss bridge in one piece, dividing the superstructure over the sea into four blocks (A to D), which were assembled on the ground and erected.
The bridge, which weighed up to 2,770 tons, was erected using cranes, but was completed in a short period of one and a half years without any accidents, and opened to traffic on March 1, 1982.
We received the Tanaka Award from the Japan Society of Civil Engineers (JSCE) and the Achievement Award from the Japan Steel Construction Association (JSIA) in 1982. The successful completion of this large-scale truss bridge gave the Bridge Division confidence, and from then on, we took on the challenge of building a wide variety of large steel structures, particularly bridges.
1985
UNLOADER WITH THE WORLD’S LARGEST UNLOADING CAPACITY INSTALLED
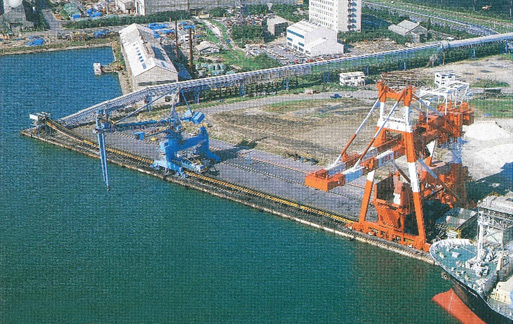
The sharp rise in oil prices caused by the second oil crisis led to a shift to alternative resources to petroleum, which again brought about a major turning point in Ube Industries' coal business strategy.
As part of the functional expansion of the call center to accommodate the increased volume of coal handled, two unloaders were built with a capacity of 2,000 tons per hour, one of the largest in the world at the time, making it possible to unload nearly twice as much coal as before.
In addition, we also improved the coal storage area by installing a stacker/reclaimer that remotely controls the loading and unloading of coal and helps prevent the dust generated by conventional truck transportation. Such mechanization has greatly increased the annual volume of coal handled at the Okinoyama Coal Center, and has firmly established its position as the largest coal handling center in Japan.
1987
ENTRY INTO AUTOMOTIVE ALUMINUM WHEEL BUSINESS
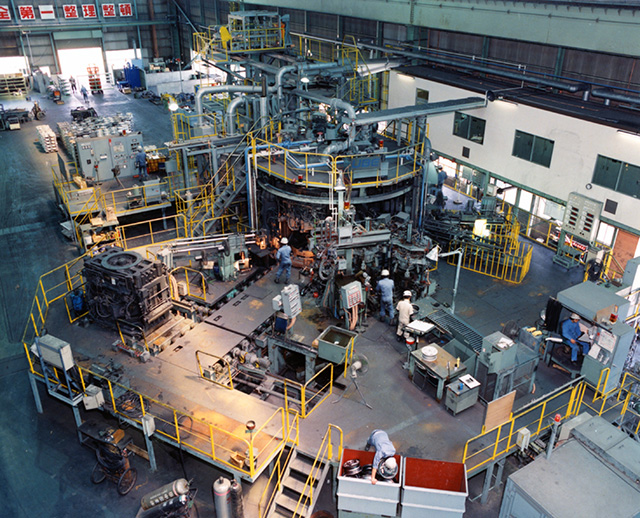
Having developed revolutionary die casting methods, such as the GF system and squeeze casting, and become one of the world's leading die casting machine manufacturers, we decided to take on the challenge of producing aluminum wheels for automobiles.
What triggered our decision was our own trial production of aluminum wheels in order to expand sales of the die casting machines for manufacturing aluminum wheels to automobile manufacturers.
As a result, we were confident that high-end aluminum wheels could be produced with the same level of design freedom and fashionability as cast aluminum wheels, and with quality comparable to the forging method. In 1987, U-mold Co., Ltd. was established, and by the following year, the company had an annual production capacity of 540,000 wheels.
In 1991, when production was back on a steady track, a plant with an annual production capacity of 1 million units (A-MOLD Corporation) was established in Ohio, US, to provide a stable supply system for the US automotive industry.
Although we have since withdrawn from the aluminum wheel business due to intensifying cost competition, the fact that we, as a BtoB machinery manufacturer, were able to make entry into a product that is directly judged by consumers is an invaluable experience that has been passed on to our business activities, including reflection on the experiences.
1996
DEVELOPMENT AND EXPANSION OF NORTH AMERICAN HUB - Establishment of UBE Machinery Inc -
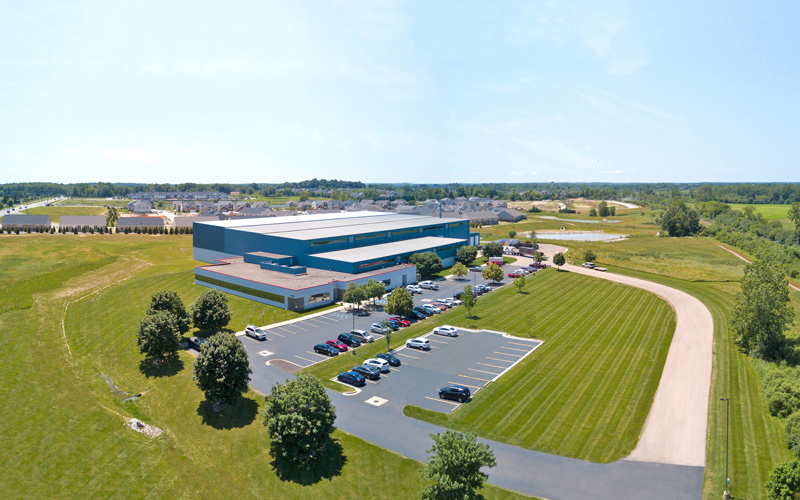
Since its early days, our molding machine business, including die casting machines and injection molding machines, has been actively exporting to U.S. companies such as the "Big Three". In order to further enhance the sales and service of these molding machines, UBE MACHINERY SALES INC. was established in 1992.
In 1996, UBE Machinery Incorporated(hereinafter: UMI) was established in Ann Arbor, Michigan, near Detroit, a center of the automotive industry, and began manufacturing die casting machines and injection molding machines in the U.S. UMI has a 105,000 ㎡ site and is capable of assembling approximately 50 large molding machines with a clamping force of 1,000 metric tons per year.
Their business activities, characterized by quick response and high quality, have won the trust of many customers, and have solidified the presence of our molding machine business in North America.
1997
"Air Floating Conveyor" NO.1 WAS INSTALLED
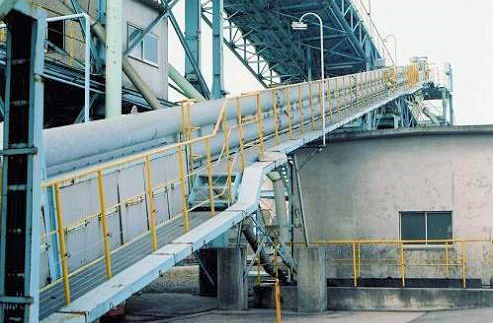
The Air Floating Conveyor (hereinafter: AFC) is a belt conveyor in which the belt is levitated by air for conveyance, and can operate with less noise and power than conventional roller type conveyors.
The completely sealed structure prevents odors from escaping and generates no dust, making it environmentally friendly.
Since the first unit was delivered to the Okinoyama Call Center in 1997, it has been delivered mainly to power plants and other large plants, and has become a representative product that demonstrates our technological capabilities.
To date, more than 130 AFC units have been sold domestically and overseas.
1998
LARGE-SIZE ALL-ELECTRIC TOGGLE-TYPE INJECTION MOLDING MACHINE "MD850S-III" DEVELOPED - Leading the world in the development of large-size electric injection molding machines -
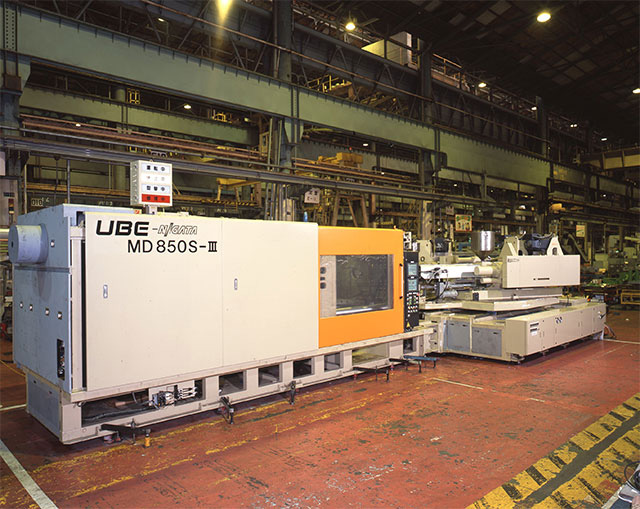
As the 21st century approached, the "century of the environment," there was a growing need for electric injection molding machines that could replace conventional hydraulic machines and reduce environmental impact by enabling high-precision, high-cycle molding as well as being low-noise, clean, and energy-efficient.
In 1998, we jointly developed with Niigata Engineering (now Niigata Machinery Co., Ltd.) a toggle-type all-electric injection molding machine with a mold clamping force of 850 metric tons, the world's largest class of all-electric machines at the time. In response to the demands of the times, we continued to lead the world in the development of larger electric injection molding machines with clamping forces of 1,000 metric tons, 1,400 metric tons, and 1,800 metric tons.
In 2005, we developed the MD3000HW, the world's largest all-electric injection molding machine with a clamping force of 3000 metric tons, which enables high-cycle and energy-saving molding of large molded parts such as automobile bumpers.
2000 - Present
We Deliver World Class Performance
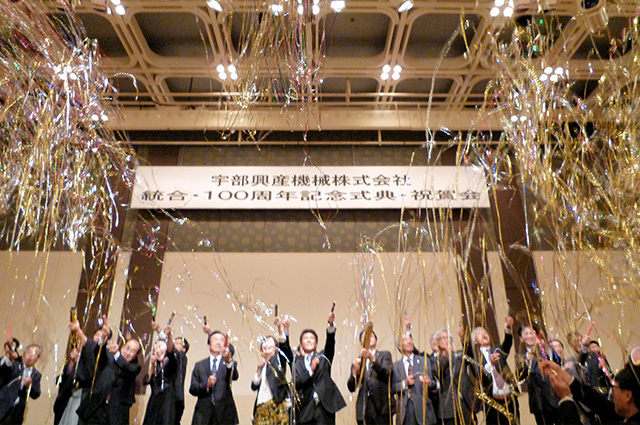
It marked a major turning point in our history, as it laid the foundation for strengthening global responsiveness and expanding service business.
At the end of the 1990s, Japan was in the midst of a prolonged recession following the collapse of the bubble economy.
In 2000, the machinery business, spun off as a separate company to ensure survival, began operations as UBE Machinery Co. In response to economic globalization, we aggressively pursued overseas expansion, alliances, and world-leading technological development.
Even in the midst of a world facing many difficult challenges, such as the realization of Carbon Neutrality and the trend toward xEVs in automobiles, we continue to endeavor to remain a valuable presence for society and customers.
2000
THE NEW "UBE Machinery Co., LTD." BEGAN OPERATIONS
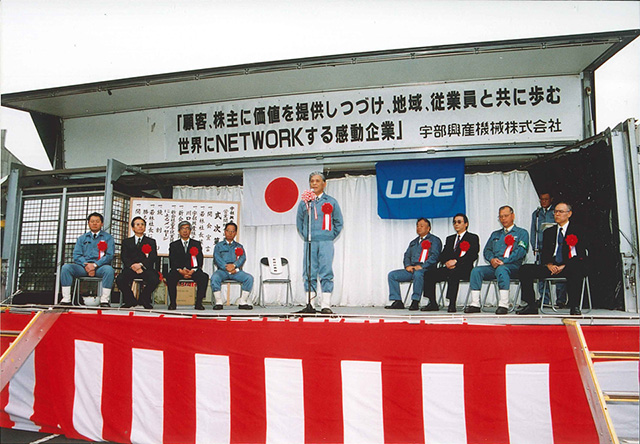
UBE Machinery Co., Ltd. was established in October 1999 as a spin-off of Ube Industries' machinery division, and began operations in April 2000.
The company's slogan at the time of its establishment was "An inspiring company that continues to provide value to its customers and shareholders, and that NETWORK to the world, working together with the community and employees."
2001
"UBE Machinery (Shanghai) Pte., Ltd." WAS ESTABLISHED - Started local production of die casting machines in China -
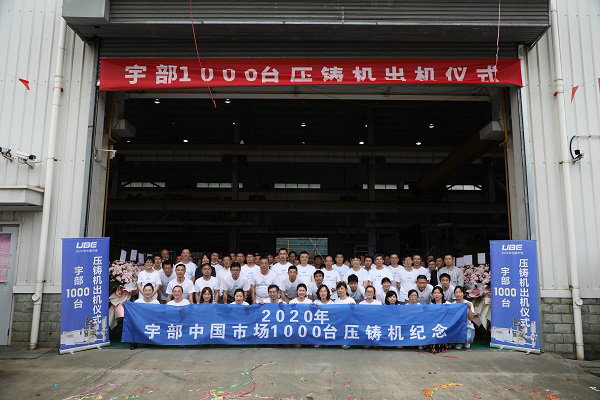
In 2001, we established UBE Machinery (Shanghai) Pte. , Ltd., a local subsidiary in Shanghai, China, which was about to join the WTO.
Our aim was to enhance the competitiveness of our products in the China market, which is expected to grow rapidly, by strengthening our brand power and presence in the market. In addition to sales and after-sales service of our products, the subsidiary is responsible for local production, OEM, technology licensing, and other operations, and has developed an integrated machinery business in China that includes production, sales, and after-sales service.
The following year, in 2002, they began local assembly of die-casting machines, establishing a tri-polar global production system for die casting machines : in Japan, the U.S., and China.
2005
"UBE Machinery Thai Co., Ltd." WAS ESTABLISHED IN THAILAND - Establishment of after-sales service base in Southeast Asia -
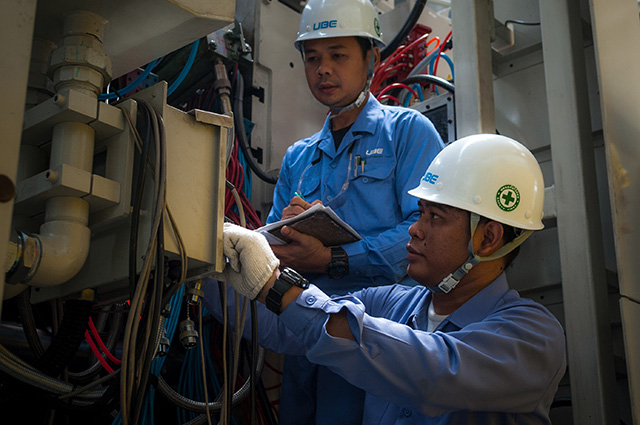
Ube Techno Eng Co., Ltd.(*), then a wholly owned service subsidiary of us, established a business base near Bangkok, Thailand as a local subsidiary to provide after-sales service business for die casting machines, injection molding machines, and extrusion presses in the Southeast Asia region.
(*) Merged with us in 2013.
2007
ESTABLISHED THE "Monozukuri Center" - Initiatives to Pass on and Improve Manufacturing Skills -
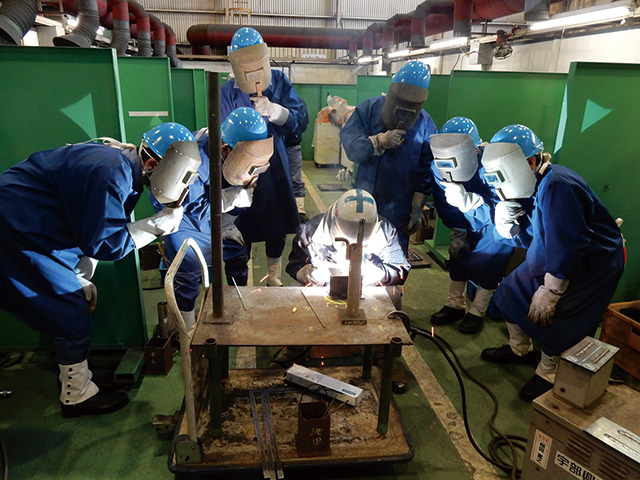
How can we create "good products"? We believe it is by constantly seeking ways to pass on and improve the excellent manufacturing skills we have inherited from our predecessors.
In 2004, we participated in the National Skills Competition for the first time, and just three years later, our representative won the bronze award in the electric welding category. In response to this achievement, 2007, we opened the "Monozukuri Center" and set up a dojo in the factory to learn machining and assembly skills as well as can manufacturing and welding skills.
2011
"UBE Machinery India Private Limited." WAS ESTABLISHED - Strengthened sales and service operations in the Indian market -
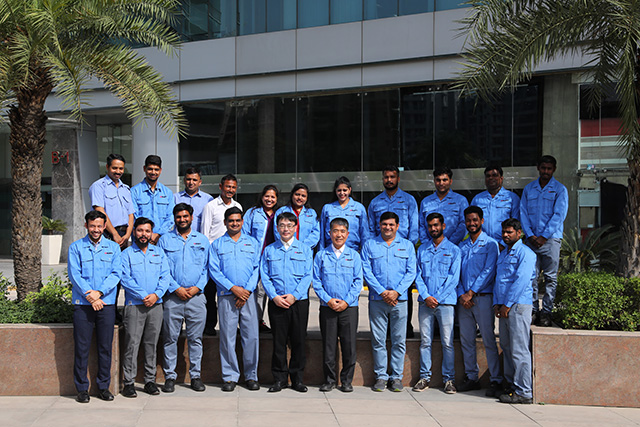
Ube Techno Eng Co., Ltd.(*) and we jointly established a subsidiary in India, which is positioned as an important market for the future due to its high economic growth rate, market size, and development potential.
By opening a subsidiary in Gurgaon, near Delhi, we have strengthened our support system for Japanese and local companies, as well as cultivated and strengthened sales in the Indian market.
(*) Merged with us in 2013.
2013
MERGED WITH "Ube Techno Eng Co." - Strengthening our ability to respond to diversified demands by integrating manufacturing, sales, and services -
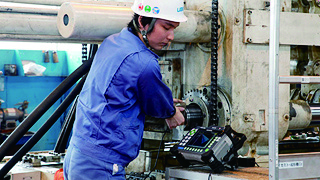
In 1977, Ube Industries Machinery Service Co., Ltd. was established to provide after-sales service to users of industrial machinery products and molding machines manufactured by Ube Machinery Works at that time, and it has been responsible for after-sales service of our products since then (the company was renamed Ube Techno Eng Co).
In 2013, we merged with the company to unify our service business and provide it to users. The aim of the merger was to further strengthen the ability to respond to diversifying demands by integrating manufacturing, sales, and services, making the most of the resources that both companies have accumulated over the years.
2014
ESTABLISHED A CAPITAL ALLIANCE WITH "TOYO Machinery & Metal Co." - Joint Development of Die Casting Machines -
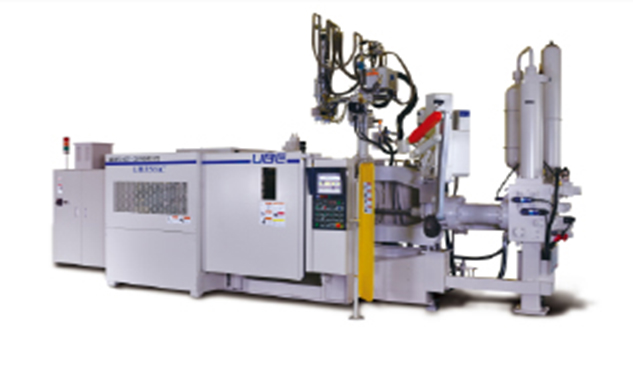
We have been cooperating with TOYO Machinery & Metal Co., Ltd. in the production of die-casting machines in China and in the development of electric type machines. In order to further deepen the cooperative relationship, both partners agreed in 2014 to enlarge the alliance in the fields of development, production, and sales of die casting machines.
Through this alliance, both companies are expected to strengthen and expand their sales on a global scale by combining their manufacturing capabilities in large-size and small-size machines and releasing new products that combine the technologies of both companies in the electric die casting machine market, which is expected to grow in the future due to its superior environmental friendliness.
The UB500iC shown in the photo is manufactured at UBE Machinery (Shanghai) Pte. Ltd.
"UBE Machinery Mexico S.A. de C.V." WAS ESTABLISHED - Strengthening the service operations in Mexico -
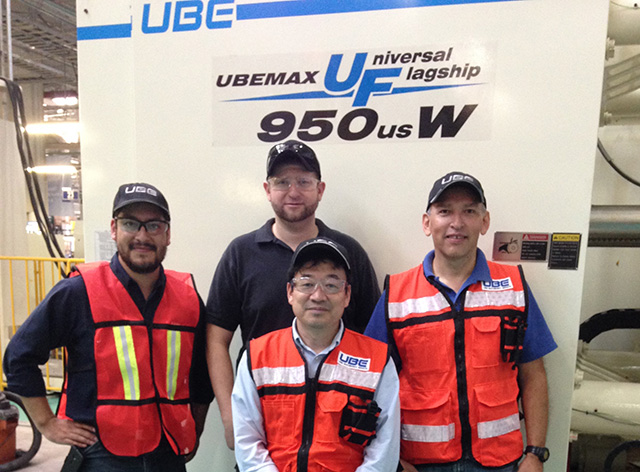
In 2014, UBE Machinery Mexico S.A.de C.V. was established in Irapuato, Guanajuato, Mexico, to provide service and maintenance for molding machines, and began operations.
The establishment of this company was prompted by the fact that automobile manufacturers at the time were actively expanding their production bases in Mexico, where they were promoting the conclusion of FTAs with other countries and finding Mexico's proximity to the U.S., the largest market, very promising.
2016
RECEIVED THE 44TH SASAKI AWARD FOR LIME KILN OIL COKE CO-FIRING TECHNOLOGY - The technology leads to fuel cost reduction in the paper pulp industry -

In 2016, Japan Technical Association of the Pulp and Paper Industry presented us with the 44th Sasaki Award for our contribution to reducing the fuel costs of the lime calcination kilns at the pulp and paper mills of various paper companies. The award commemorates Tokizo Sasaki, a businessman from the Meiji to Showa periods, and is presented once a year by the association to companies and individuals who have made outstanding achievements through technological development and research and contributed to the advancement and development of pulp and paper technology. Lime calcination kilns at paper pulp factories use much heavy oil, and reducing fuel costs has become an important issue. We proposed a technology to pulverize inexpensive oil coke (PC), a byproduct of oil refining, and have it mixed and calcined in the kiln burner, which was introduced to the paper-bulp factory.
In addition to a "vertical mill" equipped with technology to stably pulverize oil coke, Which is difficult to pulverize, our facility can burn at a high mixed combustion ratio (PC ratio: about 75%) by making full use of "kiln combustion technology" cultivated in other industries.
2017
ACQUIRED 85% OF THE SHARES OF "Mitsubishi Heavy Industries Plastic Technology Co." AND START OF BUSINESS AS "U-MHI PLATECH Co., Ltd." - Targeting to become the world's top brand of large-size injection molding machines -
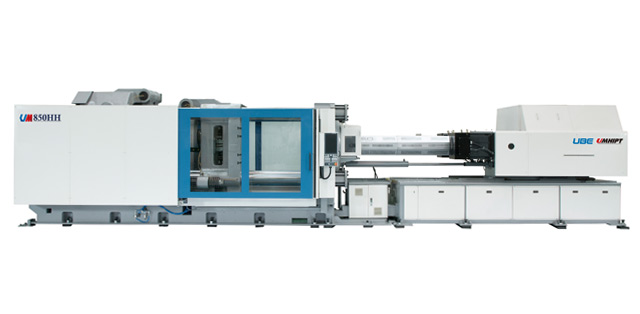
While the market for injection molding machines was steadily rising, especially in North America, China, Southeast Asia, and India, growth was not expected in Japan, and the company needed to aggressively expand overseas. With competing manufacturers in Japan, Europe, and the U.S. steadily opening bases around the world since the late 2000s, there was a growing sense of crisis as to whether we could compete on the global stage alone.
In 2015, Mitsubishi Heavy Industries (MHI), a long-time rival in the large-size injection molding machine market, approached Ube Steel, a subsidiary of us, with an offer to collaborate in the production of large-size castings. This was the catalyst for the two companies to consider a tie-up.UBE's all-electric toggle machines, which are strong in North America, and MITSUBISHI's hydraulic and electric two-platen machines, which are strong in Asia, differ in terms of their main markets and models, but the two companies had sufficient synergy and complementarity to form a relationship.
In 2017, the injection molding machine manufacturing-subsidiary of the former MHI was merged into U-MHI PLATEC Co., Ltd and U&M Plastic Solutions Co., Ltd was established to handle both companies' injection molding machines.
2018
THE U.S. BASE "UMI" EXPANDED ITS NEW ASSEMBLY PLANT FOR INJECTION MOLDING MACHINES - Toward becoming the top brand of Japanese large-size injection molding machine manufacturer in the U.S. market -
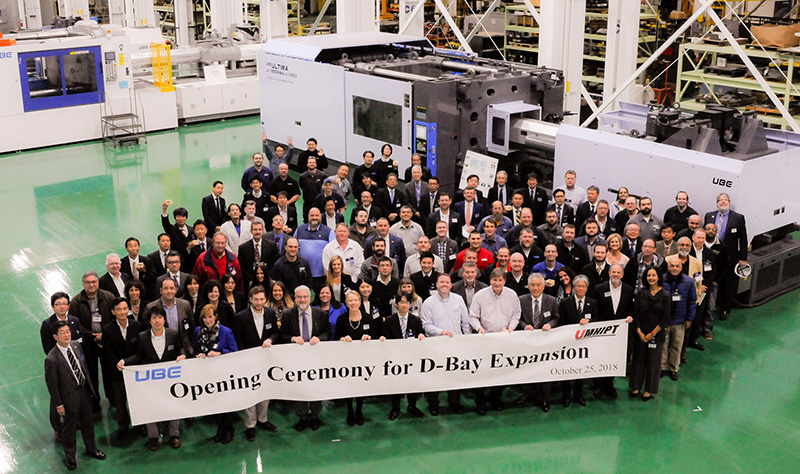
In 2018, our U.S. subsidiary UBE Machinery Inc. (Ann Arbor, Michigan; hereinafter "UMI") expanded its new injection molding machine assembly plant. UMI has been expanding sales by offering a more complete product lineup since the business integration of the injection molding machine division with U-MHI PLATECH in 2017, and in order to respond to the strong demand for space-saving large servohydraulic injection molding machines, mainly from US-based customers in recent years, it expanded the assembly plant to double the annual assembly volume of large-size machines.
This has further strengthened the group's position as the top brand of Japanese large-size injection molding machine manufacturers in the U.S.
In conjunction with the plant expansion, it has also achieved a more efficient production system and further captured the "rebuild business," in which aging equipment, such as control devices and hydraulic parts, are renewed and re-delivered with new equipment incorporating highly efficient mechanisms.
2020
TAKING OVER THE CHEMICAL EQUIPMENT BUSINESS OF "Hitachi Plant Mechanics Co., Ltd." - Toward providing high-quality products in a wider range of fields -
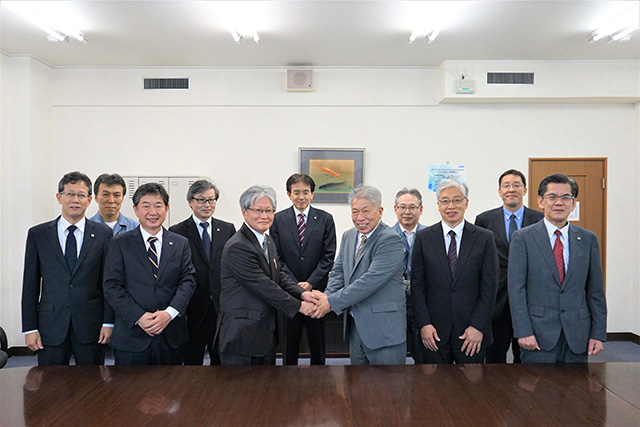
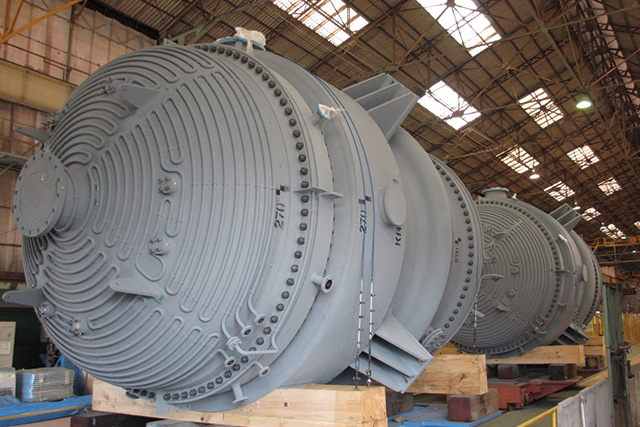
In July 2020, we took over the product and after-sales service business of chemical equipments from Hitachi Plant Mechanics Co., Ltd. We have had a cooperative relationship with them for the manufacture of chemical equipments for many years, and we have taken over their reactors, heat exchangers, thin-film evaporators, etc.
We will take over the technology, facilities, and personnel that have been cultivated by them over the years, along with the business, and provide customers in Japan and overseas with products and services of the chemical equipment business that have evolved further.
OPENING OF "Nagoya Machinery Works" - Injection molding business reorganized for business expansion -
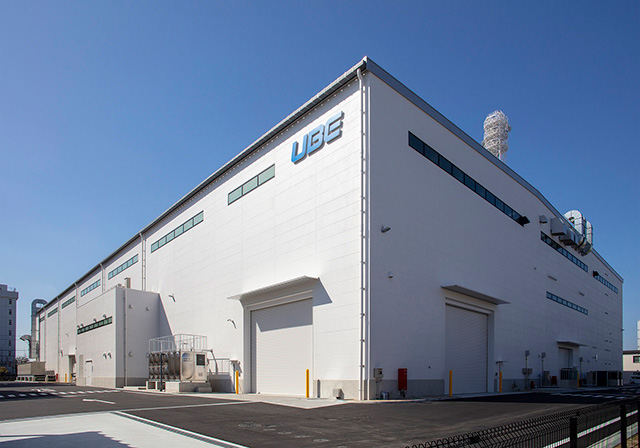
In August 2020, we merged U-MHI PLATECH and U&M Plastic Solutions and opened the Nagoya Machinery Works as a base for our injection molding business. It began operations as a state-of-the-art factory dedicated to injection molding machines, equipped with processing facilities for in-house production of screws, a key component of injection molding machines, and producing mainly the emII and emIII series of large two-platen electric machines, our mainstay models. Since our establishment in 1914 as Ube Shinkawa Ironworks, this is the first time in our more than 100-year history that a factory outside of the Ube area has been established, and we aim to expand our injection molding business by establishing a base in the Chubu region, a major center for the automobile and other "manufacturing" industries.
The IM Solution Center, which is equipped with the ability to conduct molding trials under various conditions, supports customers' product development, quality improvement, and production rationalization, and is also engaged in the research and development of advanced injection molding technology on a daily basis.
- 1914
- Ube Shinkawa Ironworks (now UBE Machinery Co., Ltd.) is established as a silent partnership.
- 1917
- Reorganized and renamed Ube Ironworks Co.
- 1924
- Supplied peripheral equipment for Ube Cement's giant kiln. This will lead to in-house production in the future.
- 1942
- Four companies with ties to Ube merge to form Ube Industries, Limited (now UBE Co.). Ube Machinery Works is established as one of the plants.
- 1953
- Screening equipment No. 1 is developed.
- 1958
- Vertical Mill (UBE-LOESCHE Mill) No. 1 is developed and delivered to Ube Nitrogen Plant. Reduction gear unit No. 1 is installed in the mill.
- 1960
- Established a technical alliance with Lake Erie Co. in U.S. for hydraulic presses.
- 1962
- Die casting machine No. 1 (850 metric tons of die clamping force) is developed.
- 1963
- The world's largest (at the time) die casting machine with a clamping force of 2,200 metric tons is developed.
- 1964
- Extrusion press No. 1 (1,650 metric tons of extrusion force) is developed.
- 1966
- Beckenbach kiln No.1 is developed.
- 1967
- The first injection molding machine (400 ton mold clamping force) is developed, and two years later, the first order is received.
- 1972
- Headquarters is moved to Okinoyama (present location) and begins operations.
- 1973
- Manufacturing of bridges and steel structures begins.
- 1976
- New injection molding machine (UBEMAX) No. 1 is developed.
- 1977
- The casting and forging division is spun off from Ube Industries to form Ube Cast & Forged Steel Co.
- 1977
- Ube Industries Machinery Service Co. is established.
- 1979
- Established a capital alliance with Fukushima Manufacturing Co.
- 1981
- No.1 indirect double-acting extrusion press for aluminum hard alloys is developed.
- 1982
- Kosan Ohashi Bridge is constructed and opened to traffic, and received the "Tanaka Award" from the Japan Society of Civil Engineers and Achievement Award from the Japan Steel Structure Association.
- 1983
- Ube Seiki Co., Ltd. is established.
- 1985
- T&U Electronics Co., Ltd. is established.
- 1986
- Squeeze casting machine No. 1, the world's first horizontal clamping and vertical casting method die casting machine, is developed.
- 1987
- U-Mold Co., Ltd. is established as an aluminum wheel manufacturing and sales company.
- 1987
- The world's largest (at the time) die casting machine with a clamping force of 4,000 metric tons is developed.
- 1989
- Ube Steel Co., Ltd. is established.
- 1992
- "100 selected bridges of Japan" Suo Ohashi Bridge, constructed.
- 1992
- UBE MACHINERY SALES INC. is established in the U.S. as a machinery sales and service company.
- 1993
- Ube Industries Machinery Service Co., Ltd. absorbs Ube Seiki Co., Ltd. and changes its name to Ube Techno Engine Co.
- 1996
- ISO9001 certification is obtained.
- 1996
- Air Floating Conveyor goes on sale.
- 1996
- UBE MACHINERY SALES INC. changed its name to UBE MACHINERY INC. UBE begins manufacturing die casting machines and injection molding machines in the U.S.A.
- 1998
- All-electric large-size injection molding machine is developed.
- 1999
- UBE Machinery Corporation, Ltd. is established by spinning off Machinery & Metal Forming Business Division of Ube Industries, Ltd.
- 1999
- Tsunoshima Ohashi Bridge (Shimonoseki City, Yamaguchi Prefecture), constructed by a consortium including us, is developed.
- 1999
- ISO14001 certification obtained.
- 2000
- UBE Machinery Corporation, Ltd. begins business.
- 2000
- Received the "Aoki Katashi" Technology Award by the Japan Society of Polymer Processing for DIEPREST molding technology.
- 2001
- UBE Machinery (Shanghai) Pte. Ltd. is established in Shanghai, China.
- 2002
- Large all-electric injection molding machine (MD-1400S III) receives the Director General's Award from the Agency for Natural Resources and Energy for its high energy-saving performance.
- 2002
- Received the 37th Japan Society for the Promotion of Machine Industry Award for the new high-cycle LeoCast molding system.
- 2005
- MD3000HW, the world's largest all-electric injection molding machine at the time with a clamping force of 3,000 metric tons, goes on sale.
- 2005
- OHSAS18001 certification is obtained.
- 2005
- UBE MACHINERY THAI Co., Ltd. is established in Bangkok, Thailand.
- 2006
- UH1250 die casting machine, equipped with a 2-platen hybrid die clamping system and the world's smallest installation space at the time, goes on sale.
- 2007
- One of our employees wins a bronze medal in electric welding at the National Skills Olympics (and will win again in 2011 and 2022)."Monozukuri Center" is established as a base for skills transfer.
- 2008
- MDS-V, a large-sized electric injection molding machine, goes on sale.
- 2010
- UB-iV series die-casting machines, designed to meet global standards, goes on sale.
- 2010
- UF Series large-sized injection molding machines, designed to meet global standards, goes on sale.
- 2011
- UBE Machinery India Private Limited is established in Gurgaon, India.
- 2012
- Established a business alliance with Toyo Machinery & Metal Co., Ltd. for the production of die-casting machines.
- 2013
- Merged with Ube Techno Engine Co.
- 2014
- Established a capital alliance with TOYO Machinery & Metal Co.
- 2014
- UBE Machinery Mexico S.A. de C.V. is established in Irapuato,Guanajuato,Mexico.
- 2014
- Hybrid Fill Casting (HFC) is developed.
- 2015
- Received the "Tanaka Award" from the Japan Society of Civil Engineers for our significant contribution to the renovation of the Gentabashi Bridge.
- 2015
- UB650iC and UB800iC medium-size die casting machines, which are jointly developed with Toyo Machinery & Metal Co. begin sales.
- 2016
- Established a comprehensive cooperation agreement with National Institute of Technology, UBE College.
- 2016
- Received the 44th Sasaki Award by Japan Technical Association of the Pulp and Paper Industry.
- 2017
- UBE acquires 85% of the shares of Mitsubishi Heavy Industries Plastic Technology Co. and establishes U-MHI PLATECH Co., Ltd. and U&M Plastic Solutions Co., Ltd. to handle UBE and Mitsubishi injection molding machines.
- 2018
- HH series mid-size electric injection molding machine is jointly developed and launched with U-MHI PLATECH Co., Ltd.
- 2018
- UBE Machinery Inc. expands its injection molding machine assembly facility.
- 2020
- The chemical equipment business is acquired from Hitachi Plant Mechanics Co., Ltd.
- 2020
- Merged with U-MHI PLATECH Co., Ltd., and U&M Plastic Solutions Corporation. Nagoya Machinery Works, the core of the injection molding business, is established.
- 2020
- SS5G, a new series of extrusion presses, goes on sale.
- 2022
- Chemical Equipment Technology Center is established.
- 2023
- New Air Floating Conveyor testing machine begins operation.