History of UBE Machinery's Injection Molding Machine
~Our long experience in the development of injection molding machines. Our DNA of technology and trust passed down from generation to generation.~
UBE Machinery's injection molding machine business has a long history that began in the 1960's. Since then, UBE Machinery has made numerous improvements and introduced many injection molding machines to the world in order to meet the high level of requirements of our customers with our exceptional creativity and comprehensive technical capabilities. As a leading manufacturer of large-size injection molding machines, we will continue to provide high-performance, high-quality injection molding machines that can be used globally, while meeting the trust and expectations of our customers.
Entering the Injection Molding Machine Industry
In the 1960s, the world was entering the plastics age. Ube Industries, which had made a full-fledged entry into the petrochemical industry, expanded its machinery business and entered the injection molding machine industry, a large market, through a technical alliance with a U.S. company.
The 1960s was a time of high growth in Japan, with the Tokyo Olympics held in 1964, and the world was entering the plastics age. Ube Industries made a full-scale entry into the petrochemical field, building plants in Japan to produce polyethylene and polypropylene resins and establishing Ube Saikon Co., Ltd. (now Techno UMG Co., Ltd.) in the United States to produce ABS resin as a joint venture with a subsidiary of U.S. auto parts manufacturer BorgWarner, Inc. Ube entered the petrochemical field in earnest. This was the heyday of consumer electronics, and many injection molding machines were being used to produce their parts.
In 1967, Ube Industries completed its first injection molding machine through joint research and development by the resin research laboratory and other in-house related divisions, and entered the industry by exhibiting the machine at the 2nd Japan Plastics Trade Fair. Ube Industries then developed a machine in a technical tie-up with BorgWarner of the U.S., the parent company of Ube Saikon's joint venture partner, and began selling injection molding machines in conjunction with ABS resin sales, winning orders from the domestic automotive industry and other customers.
This marked the beginning of UBE Machinery's injection molding business.
The roots of our Nagoya Machinery Works can be traced back to the launch of Mitsubishi Heavy Industries, Ltd.(MHI)'s injection molding machine business, the predecessor of U-MHI Platech Co., Ltd., which was integrated into our company in 2020.
1961
Nagoya Machinery Works of Mitsubishi Heavy Industries, Ltd. formed a technical alliance with NATCO (National Automatic Tool Co., Ltd.) of the U.S.
Developed "Mitsubishi NATCO Series" (Direct clamping type) machines in technical cooperation with NATCO of the U.S (Clamping force: 225-3300 tons).
The inline screw system of Reifenhäuser AG of West Germany, which NATCO introduced, became the basis of MHI's injection system.
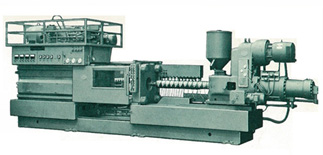
1967
UBE's first injection molding machine (Clamping force: 400 ton) completed
Developed UBE's first injection molding machine "UD Series" with direct pressure and in-line screw system.
In-house production by Ube Iron Works, Machinery Division, Ube Industries, Ltd.
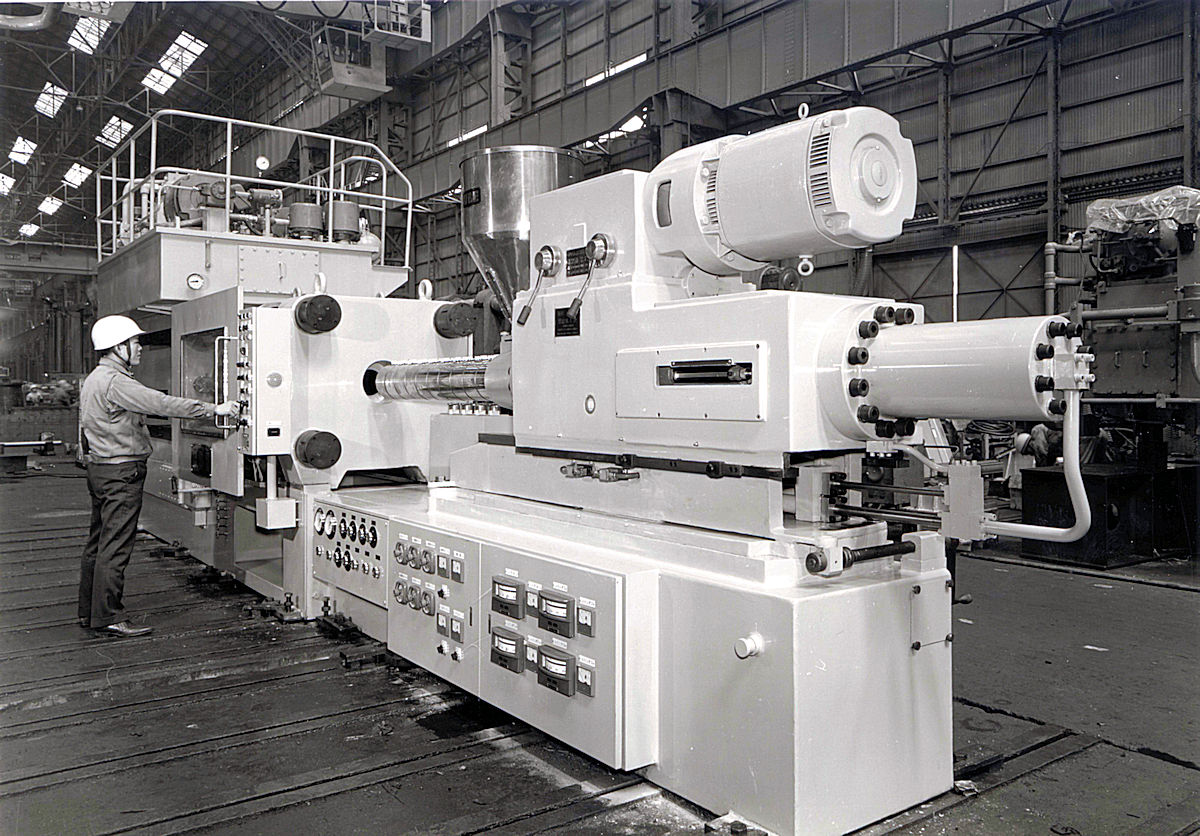
Ube Industries, Ltd. and BorgWarner, Inc. of the U.S. enter into a technical tie-up
Ube Industries developed the "BW Series" (Direct clamping, Screwless type) under a technical tie-up with BorgWarner of the U.S. (Clamping force: 250 to 800 tons).
Practical application of the screwless system that "utilizes the shear heat generated by the resin itself," which was considered the ideal resin plasticizer at the time.
1968
Buir Machinery (Buir Masehinenbau GmbH) established in West Germany.
Developed local production of small machines and sales in Europe (-1975).
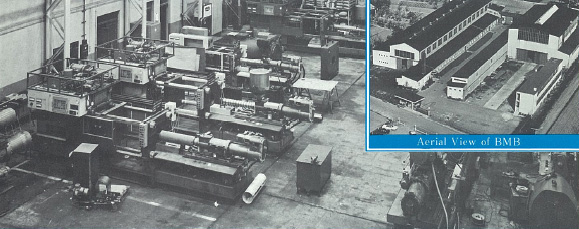
Developed the world's first transistor control device and installed it in an injection molding machine
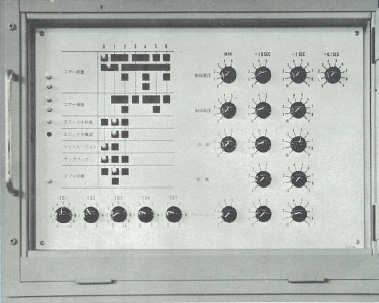
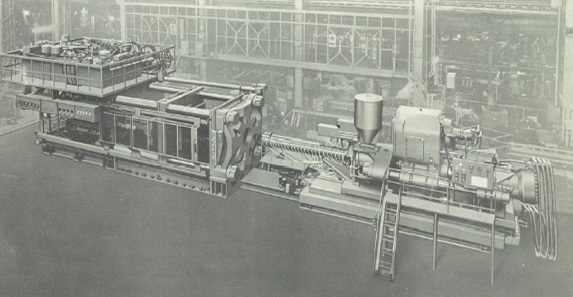
Clamping force: 3300 tons
Injection capacity: 1000 oz.
Overall machine length: 21m
Application: Plastic Pallet
1969
Development of Large-sized Injection Molding Machine with Toggle Clamping System
Developed the world's first toggle type "BWT Series" large-sized injection molding machine by utilizing our experience with die casting machines. (Clamping force: 800 to 2000 tons)
Received orders from the domestic automotive industry, etc.
Equipped with our patented "Tiebar Puller" technology that contributes to more efficient injection molding.
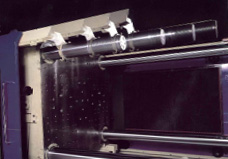
Going the Way of Independent Development
After entering the market and winning orders, Ube Industries was faced with a series of returns due to a flaw in the design of a U.S. manufacturer with whom the company had a technical tie-up. We overcame this difficult situation by making improvements within our facilities and embarking on a path of independent development, expanding sales of large injection molding machines and securing our position in the industry.
Ube Industries, which was not well known as an injection molding machine manufacturer, borrowed the global name brand of U.S.-based BorgWarner and won orders mainly from the domestic automotive industry. However, the BW series, a machine developed in technical cooperation with BorgWarner, had several problems that needed to be improved, and in order to regain the trust of our customers, we desperately made a number of improvements to the machine on our own. First, to solve the problem of the direct clamping type mold clamping device of the BW series, we adopted a toggle type mold clamping device, which had a proven track record in large die casting machines, and developed the world's first toggle type large injection molding machine, the "BWT series". In 1976, we further improved the malfunction of the injection device and independently developed and delivered the "UBEMAX Series," a versatile inline screw type that meets the needs of customers.
Having overcome this difficult situation by embarking on a path of independent development, we took advantage of the shift from polyurethane resin to polypropylene resin as a material for automotive bumpers and expanded sales of large-size injection molding machines to the automotive industry. This secured Ube Industries' position in the injection molding machine industry.
1976
Released the first model of the UBEMAX Series, an independently developed toggle type injection molding machine
(Clamping force: 200-4200 tons)
Independently developed and equipped with toggle type mold clamping device, versatile cross-wave screw, etc.
Expanded sales of large-sized injection molding machines mainly to the automotive industry, securing Ube Industries' position in the injection molding machine industry.
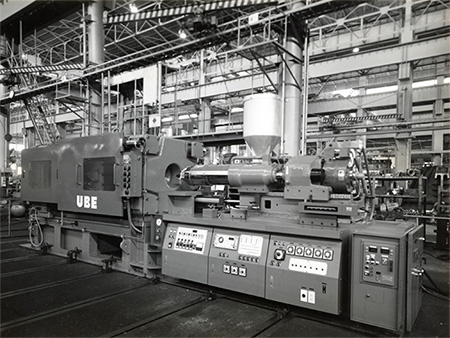
1976
Completed "MD Series" direct-clamping injection molding machine developed independently
(Clamping force: 350 to 2450 tons)
Equipped with new mechanisms such as multi-stage injection control and process control device
MHI's direct-clamping series had been changed to MF, MG, MSG, MMG, and MGV.
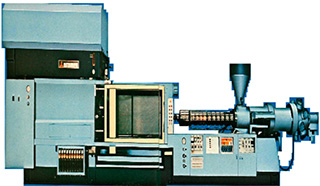
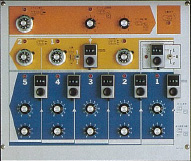
Expansion into the U.S., a huge market
With the end of high economic growth and declining demand in Japan, we entered the huge U.S. market.
As a result of our continuous improvements in response to the strict demands of Japanese automakers, who were following in the footsteps of the U.S. Big Three, our automation technology has been highly evaluated, and we have received large orders from GM and Ford.
In 1984, we opened a U.S. service center and established the foundation of our North American business.
Around 1973, when the oil crisis hit, Japan's rapid economic growth ended. With no prospect of expanding demand in the Japanese market and a decrease in the number of machines being added to the plants in Japan, we embarked on an expansion into the huge U.S. market.
Japanese automakers, which were inferior to the U.S. Big Three in terms of management and technology in the early 1960s, desperately worked on improvement activities such as streamlining and labor saving, and caught up with and surpassed the U.S. automakers in about 10 years. By gritting its teeth to meet these strict demands of the Japanese automakers, our machines also accumulated improvements, enabling it to overtake the machines of U.S. manufacturers and enter the U.S. market.
In the 1980s, following presses and die-casting machines, we received large orders for injection molding machines from two of the "Big Three" U.S. automakers, Ford and GM, which were the result of UBE Machinery's highly regarded technology, including a "single setup" machine that could change molds in five minutes. In 1984, UBE opened a service center in Ann Arbor, near Detroit, the home of the Big Three. UBE's customer-oriented approach to service was further recognized and continued orders were received, laying the foundation for UBE Machinery's North American business today.
1978
Establishment of UBE Industries (America) Inc.
First U.S. office established in New York City for sales and service of UBE products.
1980
Development of highly mixing "UB SCREW"
Screw with double flight design realizes excellent plasticizing performance such as high mixing and high plasticizing capacity.
The development of the "UB (Ultra Barrier) Screw" was made possible by the introduction of a method of cooling and solidifying the resin in the groove and taking samples in screw research.
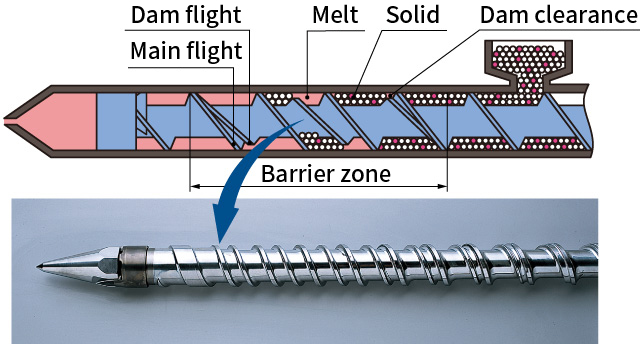
1984
UBE Industries America Michigan Branch (Ann Arbor) opens
Establishes a service base for the molding machine business in Ann Arbor, near Detroit, USA, laying the foundation for today's North American business.
Receives large orders from the U.S. Big Three automakers, Ford and GM.
1992 Michigan branch becomes independent as UBE MACHINERY SALES INC. and expands office and warehouse
1996 Company name changed to the current "UBE MACHINERY INC."
Constructed a manufacturing plant to provide engineering, manufacturing, and support services, and began assembling die casting machines and injection molding machines.
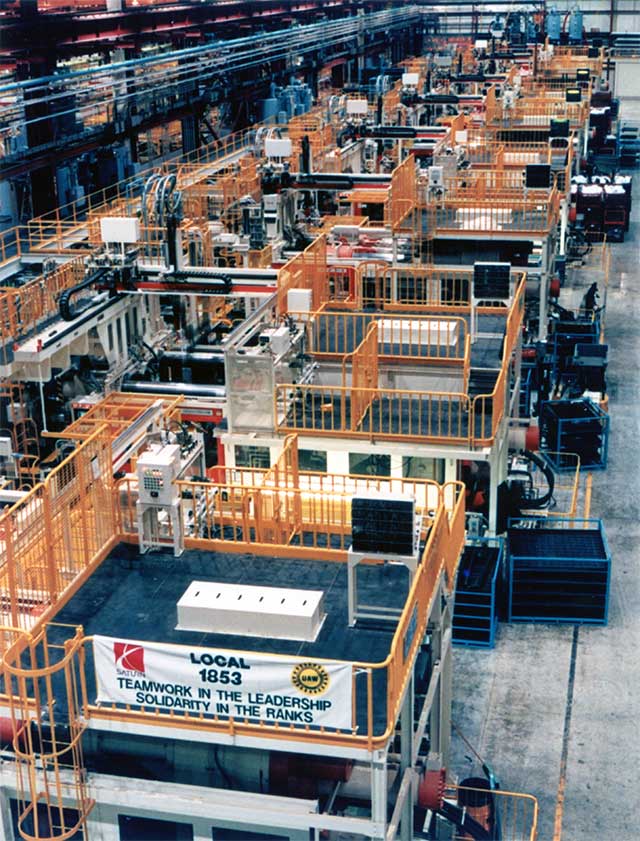
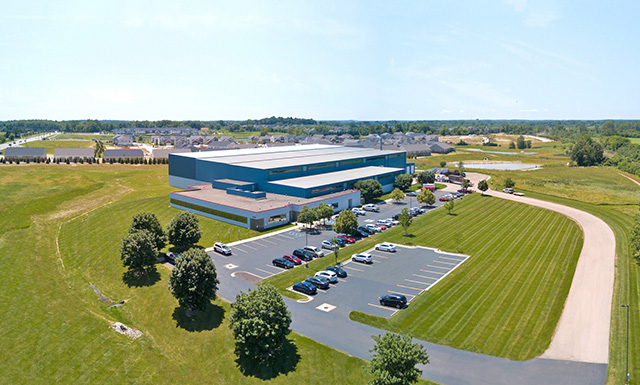
(Ann Arbor, Michigan)
Challenges in response to diversifying needs
In the 1980s, as people's lives became more affluent, we aggressively took on the challenge of developing new models in response to the diversification and larger size of plastic products in many industries. We launched a succession of advanced machines, and this has formed UBE Machinery's current strength of "large injection molding machines that meet the high value-added needs of our customers".
As the Japanese economy has stabilized after two oil shocks and trade friction between Japan and the U.S., and people's lives have become more affluent, a wide variety of plastic products are now used in many industries, including automobiles, home appliances, OA communication equipment, housing equipment, and industrial materials.
In order to increase sales of medium- and large-sized injection molding machines, which are our forte, we took on the challenge of developing new models to accommodate the increasingly diverse and large-sized applications for plastic molded products, and launched a series of advanced injection molding machines that were multifunctional, high-cycle, energy-saving, and space-saving.
This was the time when UBE Machinery's current strength of "large injection molding machines that meet customers' high value-added needs" took shape.
Medium and Large-sized hydraulic injection molding machines developed one after another
Expanded line-up to meet diversifying applications and needs.
In addition to the medium-sized toggle type "PZ Series," large-sized toggle type "ST Series," and space-saving large-sized hydro-mechanical clamping type "UU Series," "LM Series" for thermosetting resin and "SZ Series" for two-stage molds were developed for special applications.
Development and installation of the high-precision, full-response controller "HUMMA" that flexibly links man and machine.
1984
Entered the small machine field with the independently developed compact direct-clamping type "MS Series"
(Clamping force: 225 to 290 tons)
MHI's small-sized hydraulic injection molding machines had been changed to the MS II, MSP, MS III, and MSV Series.
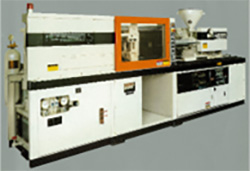
1985
Medium-sized toggle type hydraulic injection molding machine "PZ Series" developed
(Clamping force: 250 to 900 tons)
Medium-sized injection molding machine with high versatility, high cycle molding, and high cost performance.
The series had been changed to PZ II and PZ III in pursuit of user-friendliness and energy-saving performance.
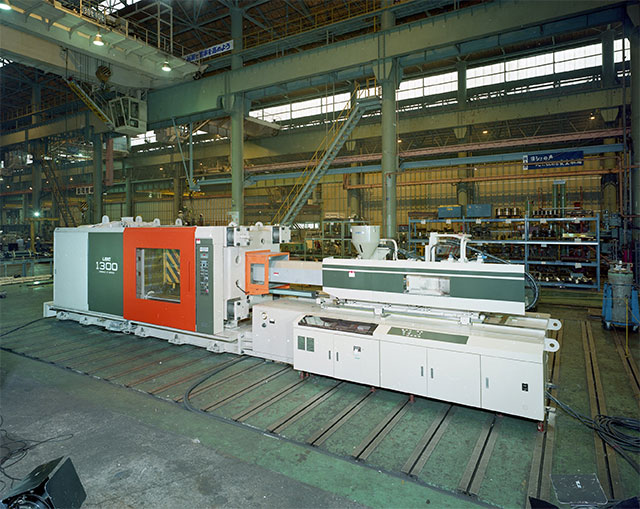
1986
Large-sized toggle type hydraulic injection molding machine "ST Series" developed
(Clamping force: 1000 to 6300 tons)
Large-sized injection molding machine with multiple functions, high cycle time, and energy-saving features to meet the needs of larger molded product applications.
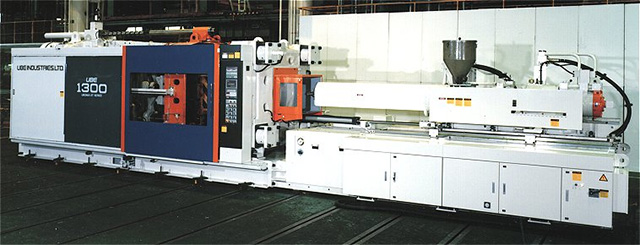
1987
Space-saving medium and large 2-platen hydraulic machine "MM Series" developed
(Clamping force: 1300 to 5000 tons)
Prototype of the large two-platen hydro-mechanical clamping type injection molding machine currently manufactured at our Nagoya Machinery Works.
Expanding the market with space-saving machines equipped with the world's first 2-platen clamping mechanism.
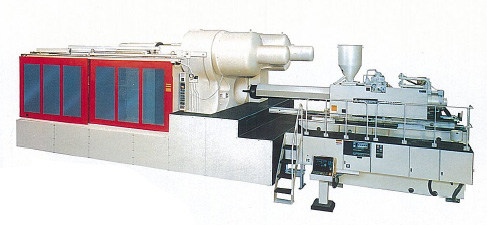
1989
Development of ultra-compact direct clamping hybrid electric clamping system "MSS Series"
(Clamping force: 15 to 50 tons)
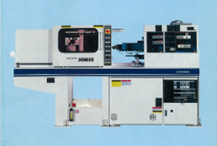
1990
Developed space-saving large-sized hydro-mechanical clamping type injection molding machine "UU Series"
(Clamping force: 1300 to 4000 tons)
High-performance machine with a compact design and increased flexibility in equipment planning for large machines.
Transition to the UU II Series of composite clamping servo-hydraulic injection molding machines launched in 2015.
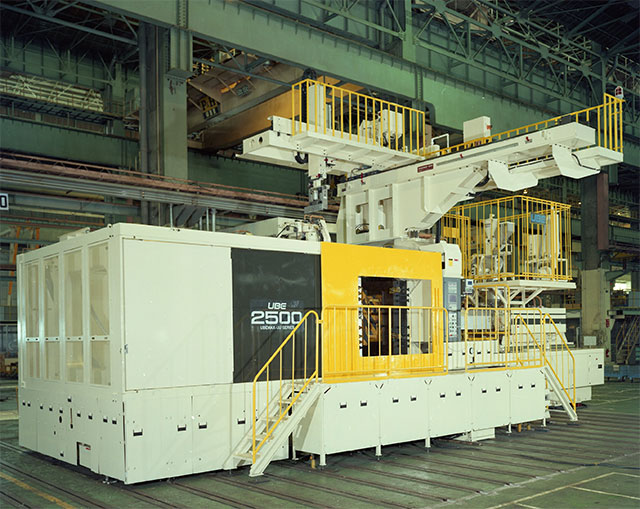
1995
Developed space-saving large 2-platen hydraulic machine "MMⅢ Series"
(Clamping force: 1300 to 4000 tons)
Best-selling machine with an extensive delivery record in the global market, improved from the MM Series.
Transitioned to the current MMV Series with minor changes.

Developing World-Leading Large Electric Machines and Approaching Emerging Markets
As the 21st century approached and environmental measures such as energy conservation became more pressing, we developed the world's largest electric injection molding machine at the time, and was among the first to develop the electrification of large machines and molding processes. In addition to the North American market, we began to approach emerging markets such as China and Southeast Asia, where demand was increasing. UBE Machinery established its brand as "the world's leading manufacturer of large-sized injection molding machines with technological prowess".
After overcoming the oil crisis, the world had shifted to energy-efficient industries and energy-conscious lifestyles, and the 21st century, the century of the environment, had called for global environmental protection efforts on all fronts. The plastic molding and processing industry was no exception to this trend, and there was an urgent need for energy-saving and environmental load reduction measures through the improvement of molding machines and molding technologies.
Against this backdrop, the injection molding machine industry in Japan had been shifting from conventional hydraulic-driven machines to "electric-driven machines", which offered energy savings, low noise, cleanliness, and other environmental benefits, as well as improved productivity through high-cycle molding and precision molding with high repetition accuracy. In response to the needs of products such as cell phones, notebook PCs, optical discs, and medical-related products, which required particularly strict dimensional accuracy and optical characteristics, the development of electrically-driven small injection molding machines took the lead.
In this environment, we were quick to take advantage of its technological expertise accumulated through the development of large-sized injection molding machines to develop electric-driven large-sized injection molding machines and molding processes that take advantage of the superior characteristics of electric machines.
In addition, we began approaching emerging markets such as China and Southeast Asia, where demand for large injection molding machines was increasing, particularly in the consumer electronics and automotive industries, and promoted manufacturing and sales alliances with major Chinese injection molding machine manufacturers.
At the turn of the 21st century, UBE Machinery established its brand as "the world's leading manufacturer of large-sized injection molding machines with technological prowess".
1998
Large-sized toggle type all-electric injection molding machine "MD850S-III" developed
Jointly developed with Niigata Engineering Co, Ltd. (now Niigata Machinery Co., Ltd.)
"MD-III Series" toggle type all-electric injection molding machine with 850 tons of mold clamping force, the world's largest class of all-electric machines at the time. (Clamping force: 650 to 1800 tons)
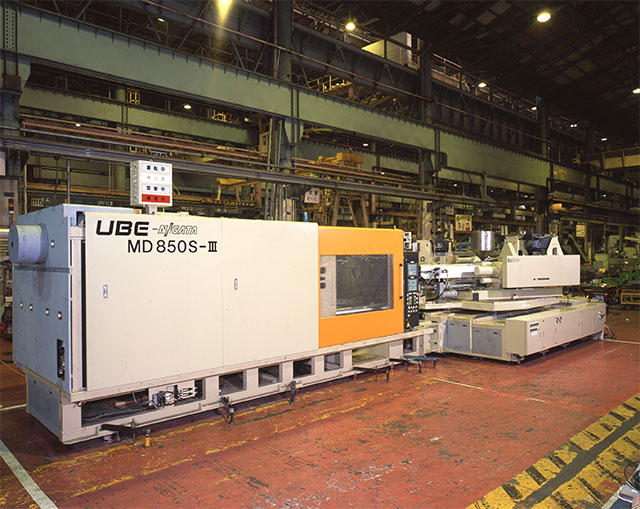
1999
UBE Machinery Announces "DIEPREST Molding Process," a Technology for Integrated Molding of Skin Material
UBE Machinery's proprietary molding process developed by combining skin material insert and low-pressure injection molding technologies, which is the result of R&D activities that take advantage of our unique position as a plastics and machinery manufacturer.
Realization of high performance and composite molding by ultra-precise mold opening/closing control.
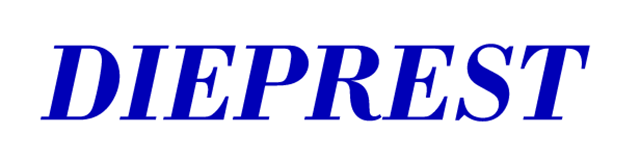
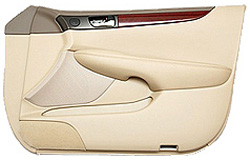
(Automotive interior parts)
1999
Medium-sized toggle type all-electric injection molding machine "ME Series" developed
(Clamping force: 350 to 550 tons)
Full-scale entry into the electric injection molding machine market with the "MAC-VIII" controller.
Developed MHI's first toggle type clamping mechanism. The series was further improved and changed to ME II and ME III.
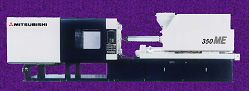
2000
Received the "Aoki Katashi Technology Award" from the Society of Plastic Molding and Processing Engineers of Japan for "DIEPREST Molding Technology".
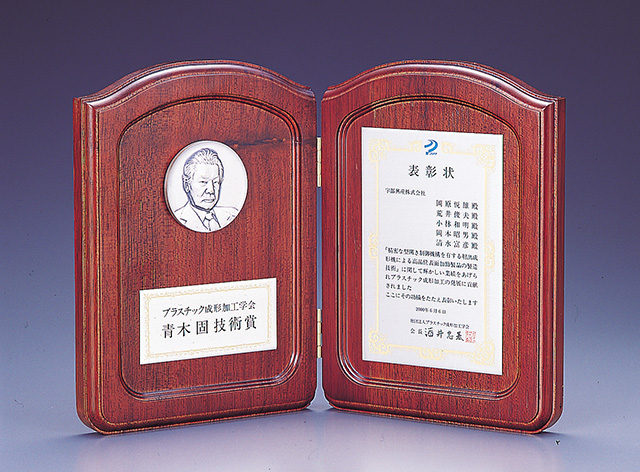
Received the Aoki Katashi Technology Award from the Japan Society of Polymer Processing
2000
Sales tie-up with FANUC Corporation; domestic sales of small-sized toggle type all-electric injection molding machines begin (Clamping force: 15 to 300 tons).
2001
Developed space-saving, medium and large-sized 2-platen electric injection molding machine "em Series" (Clamping force: 650 to 3000 tons)
World's first 2-platen electric injection molding machine, the origin of the current em II and em III Series.
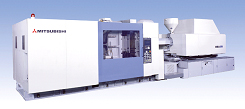
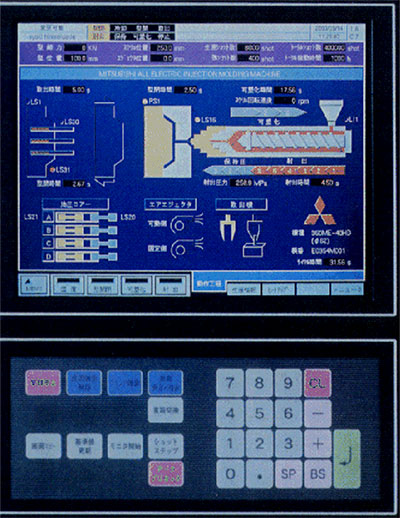
"MAC-VIII" controller receives Good Design Award in Japan
2002
Large-sized toggle type all-electric injection molding machine "MD1400S-III" receives the Director General Prize of Agency of Natural Resources and Energy
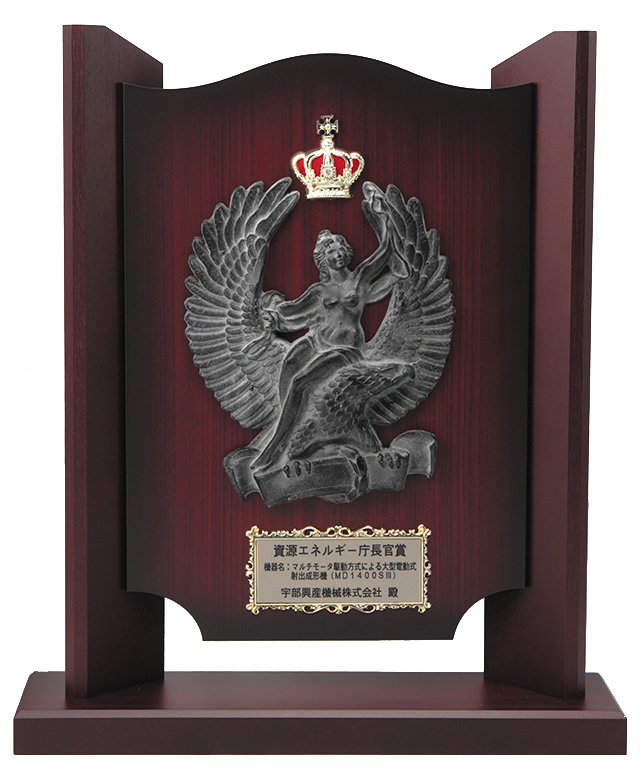
UBE MACHINERY Licenses Hydraulic Injection Molding Machine Technology to China's Wuxi Grand Tech Machinery Co.,Ltd.
Strengthened sales capabilities in the Chinese and Asian markets by teaming up with Wuxi Grand Tech Machinery Co.,Ltd. under the Cosmos Machinery Group of Hong Kong.
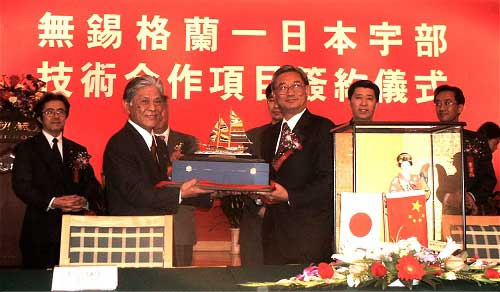
2002
OEM sales tie-up with Toyo Machinery & Metal Co., Ltd. to begin overseas sales of "MEt Series" of small-sized toggle type all-electric injection molding machines
(Clamping force: 30 to 280 tons)
Developed "SCS molding" for family molds
2003
"MD-IV Series" large-sized toggle type all-electric injection molding machine developed
(Mold clamping force: 650 to 3000 tons)
Further evolved from the "MD-III Series," the "MDS-IV Series" offers significantly improved quality and functionality, contributing to high-value-added molding.
2003
Development of the "MEⅡ Series" medium-sized toggle type all-electric machine
(Clamping force: 350 to 850 tons)
Equipped with a direct drive (DD) servo motor developed exclusively for injection.
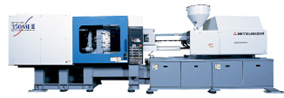
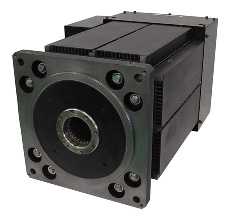
2004
Developed the world's largest space-saving ultra-large-sized 2-platen electric machine "3000em"
"Center press mold clamping" for burrless molding.
DD servo motor mounted on injection unit.
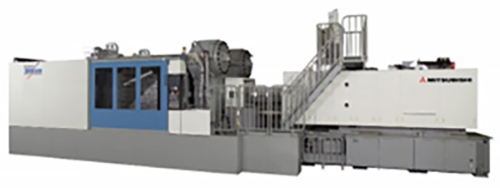
2005
Developed "MD3000HWS-IV", one of the world's largest ultra-large-sized toggle type all-electric injection molding machine
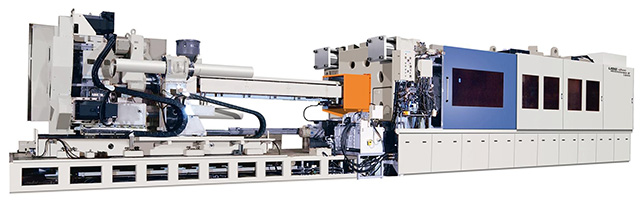
2005
Establishment of Mitsubishi Heavy Industries Plastic Technology Co., Ltd.
Injection molding machine business spun off from Mitsubishi Heavy Industries, Ltd.
2006
Development of Ultra-Large-sized electric 2-material rotary molding machine "3000emR"
"emR" Series (Clamping force: 1450, 3000 tons)
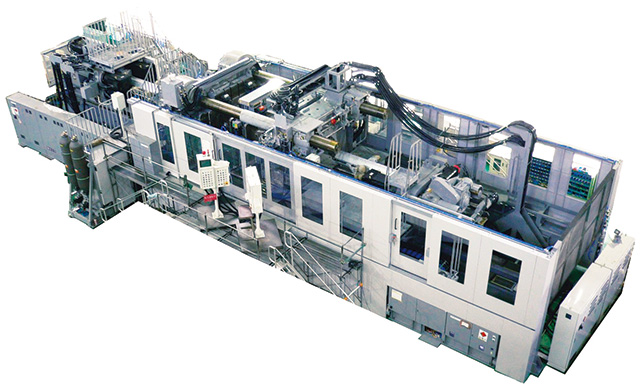
3000em receives the Machine Design Award and the Judge's Special Award in Japan
2007
Establishment of Wuxi Ube-Cosmos Machinery Ltd.
Joint venture with China's Wuxi Grand Tech Machinery Co.,Ltd. to produce hydraulic injection molding machines in China.
Strengthened alliance to expand the Chinese market for large-sized injection molding machines in line with the development of the Chinese automotive industry.
2008
"MDS-V Series" large-sized toggle type all-electric injection molding machine developed
(Clamping force: 650 to 3500 tons)
With "Value Innovation" as the keyword, the basic performance of the all-electric injection molding machine has been greatly innovated to achieve improved performance.
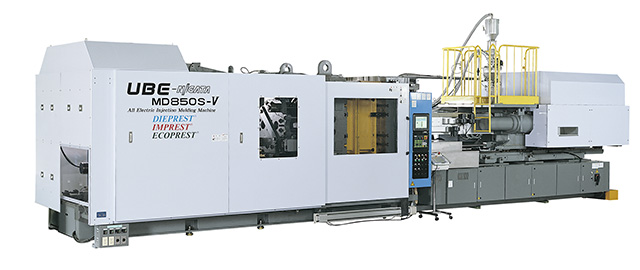
2008
Large-sized 2-platen electric injection molding machine "em II Series" developed
(Clamping force: 1050 to 3500 tons)
High-end machine that meets various needs such as high value-added molding realized by industry's top-class high performance.
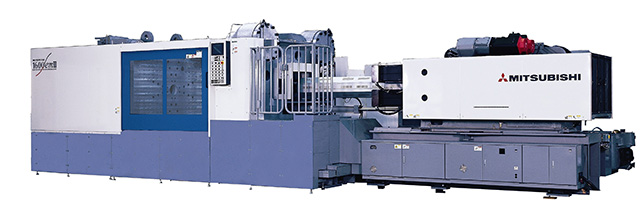
2010
Large-sized toggle type all-electric injection molding machine "UF series" developed
(Clamping force: 650 to 3500 tons)
Equipped with the easy-to-operate "e-HUMMA" controller, a global standard machine that thoroughly pursues ease of use.
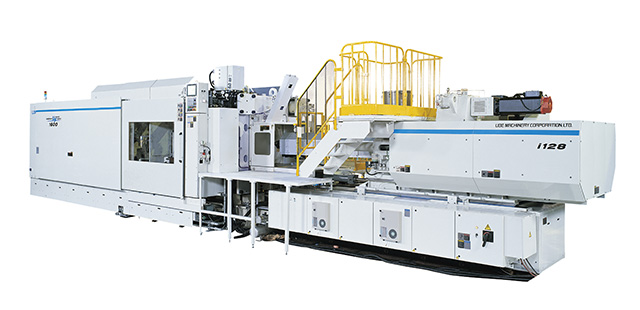
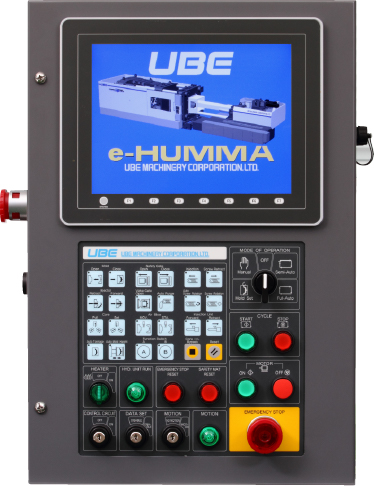
2011
OEM production tie-up with China's Chen Hsong Group for large-sized servo-hydraulic machine "MMX Series"
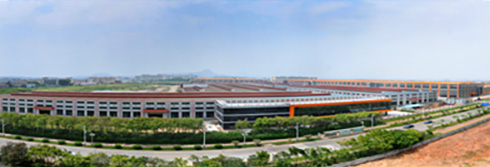
2012
Development of the "MMX Series", large-sized 2-platen servo-hydraulic injection molding machines
(Clamping force: 1050 to 3500 tons)
Space-saving servo-hydraulic machine that achieves production cost reduction, energy saving, and high cycle molding, and promises high reliability.
Critical functional parts are made in Japan and Europe, and MHI's thorough quality guidance and management ensure Japanese good quality even under global production.
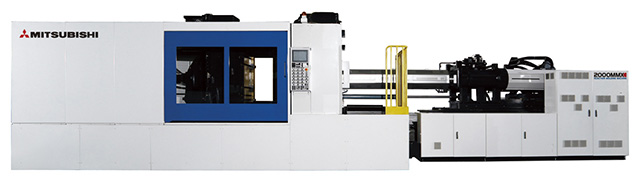
2013
Licensed all-electric injection molding machine technology to China's Cosmos Machinery Technology (Jiangsu) Co.,Ltd.
Expanded alliance with Cosmos Machinery to develop and expand sales of all-electric machines for the Chinese market.
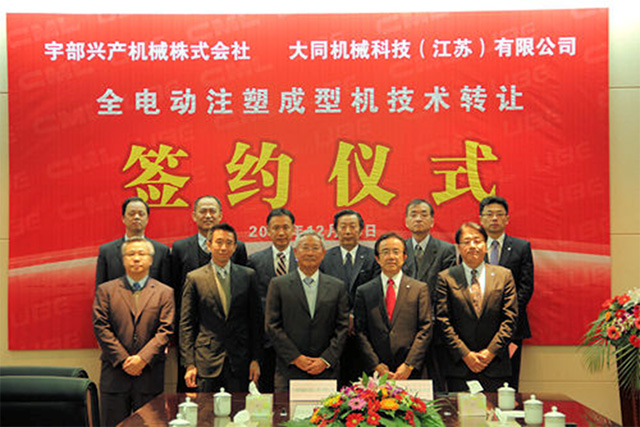
2015
Large-sized composite clamping servo-hydraulic injection molding machine "SERVOMAX UU II Series" developed
(Clamping force: 2500,3000 tons)
Evolution of the space-saving "UU Series" machine, equipped with a servo-hydraulic pump for energy-saving performance.
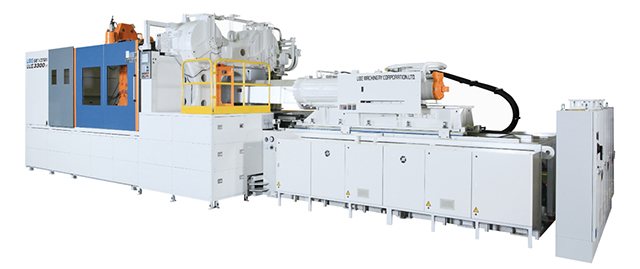
"SERVOMAX US series" large-sized toggle type servo-hydraulic injection molding machine developed
(Clamping force: 900 to 2200 tons)
Large-sized UBE Machinery's toggle type machine with a proven track record is equipped with a servo-hydraulic pump for energy-saving performance.
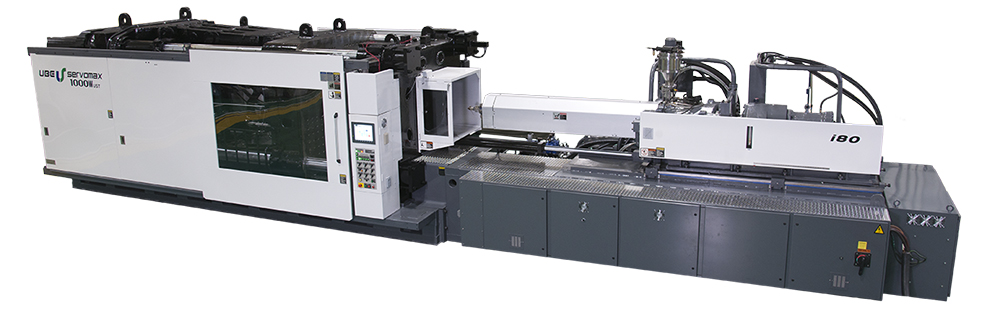
2015
Development of direct fiber blending and molding system "1300emII-DLFT"
Long fiber material and compound-less resin are directly blended in the injection molding machine to produce lightweight, high-strength products at low cost.
Developed "MAC-IX, the Connected Controller".
High-speed, high-precision control that realizes outstanding operability with two large independent screens and the concept of IoT.
Developed a medium-sized toggle type all-electric injection molding machine "ME III Series"
(Clamping force: 350 to 850 tons).
The ME II series, which was equipped with the MAC-IX controller and had a proven track record in global production, has been further evolved.
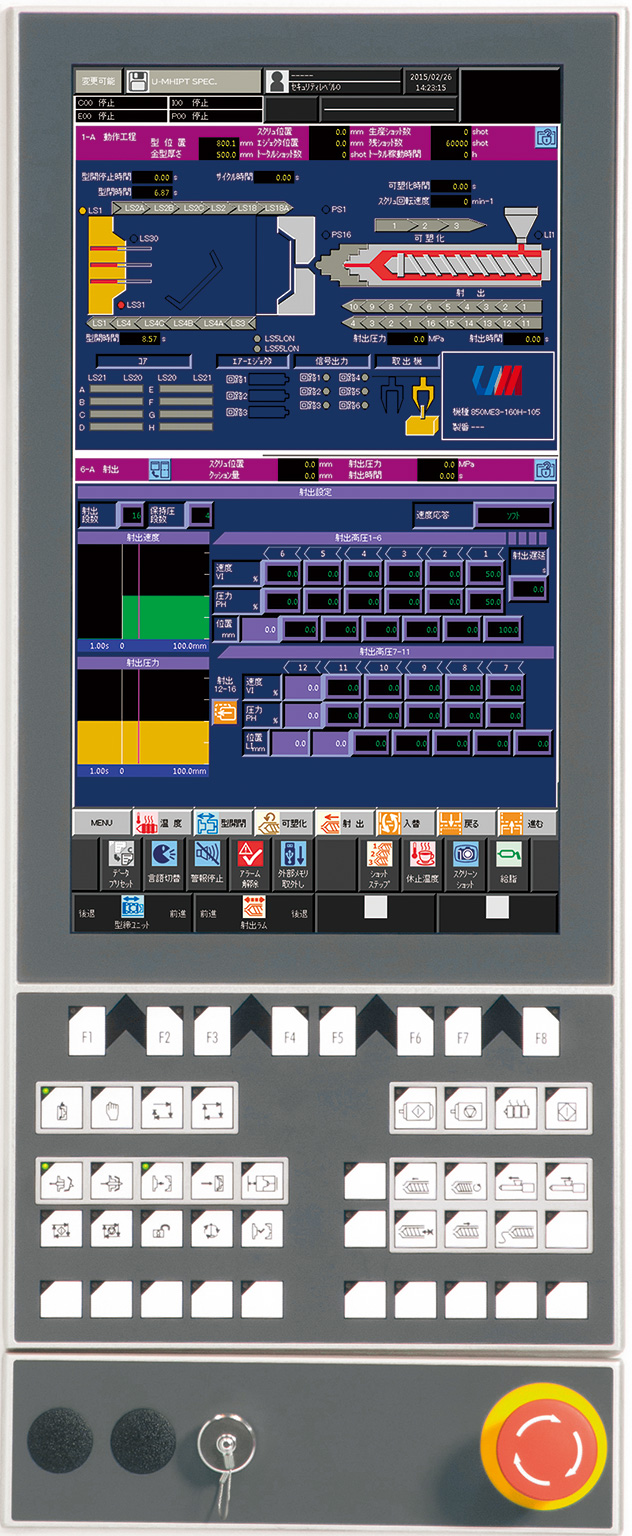
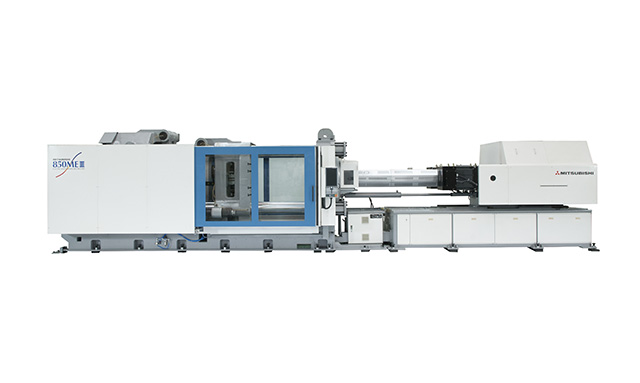
Aiming to be the world's top brand of large-sized injection molding machines
Amid increasingly fierce competition with global competitors in the expanding global market, in 2017, the injection molding machine subsidiary of Mitsubishi Heavy Industries, a long-time rival in large-sized machines, was placed under the UBE Machinery Group umbrella. The two companies continued to combine their "strengths" and fully integrated their operations in 2020, opening our Nagoya Machinery Works. The reorganization of UBE Machinery's injection molding machine business has been completed, and we are now ready to become the world's top brand in large-sized injection molding machines.
While the injection molding machine market was growing steadily in North America, China, Southeast Asia, India, and other regions, we could not expect growth in Japan and needed to aggressively expand overseas. In the late 2000s, competing manufacturers in Japan, Europe, and the U.S. began steadily opening bases around the world.
In 2015, Mitsubishi Heavy Industries(MHI), a long-time rival in the injection molding machine market for large-size machines, approached Ube Steel Corporation, a UBE Machinery Group company, about collaboration in the manufacture of large-size castings.This was the catalyst for the two companies to consider a tie-up.
In the past, the two companies were often competitors in the large injection molding machine businesses, and there was a sense of tension between them, not knowing when the other would get a foothold, but as we shared the same sense of crisis and discussed the possibility of an alliance, they became more convinced than ever that they could build a win-win relationship.
Although both companies were engaged in the same large-sized machine business, "Ube, with its all-electric toggle machines strong in North America," and "Mitsubishi, with its hydraulic and electric 2-platen machines strong in Asia," had different core markets and different models, and the two companies had sufficient synergy and complementary relationship.
In 2017, we acquired MHI's injection molding machine subsidiary and integrated its operations under the UBE Machinery Group, and in 2020, we merged that subsidiary into our company to achieve full integration and open a new plant, Nagoya Machinery Works, marking the start of a new structure for our injection molding machine business.
UBE Machinery has taken the first step toward becoming a machine manufacturer that can compete globally in our main battlefield of large injection molding machines.
2017
On Jan. 1, acquires 85% of the shares of Mitsubishi Heavy Industries Plastic Technology Co.,Ltd.
Merge with Mitsubishi Heavy Industries' injection molding machine business in order to expand business in the global market
U-MHI Platec Co., Ltd., a Ube Machinery Group company, begins operations

"U&M Plastic Solutions Co., Ltd." established as a sales company to handle injection molding machines from both Ube Machinery and U-MHI Platech, and begins operations.
The service division of the injection molding machine business of Mitsubishi Heavy Industries America, Inc. is transitioned and established as "U-MHI Platech America, Inc." as a U.S. service subsidiary of U-MHI Platech.
(Sales division of injection molding machine business of Mitsubishi Heavy Industries America, Inc. is integrated into UBE MACHINERY, INC. in the U.S.)
Ube Machinery and U-MHI Platech to jointly exhibit at "IPF Japan 2017 International Plastic Fair" under the theme of "Fusion"
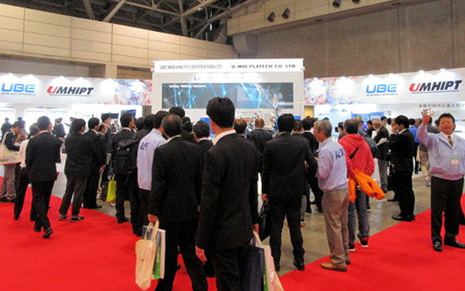
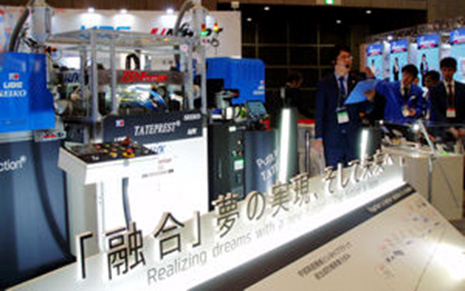
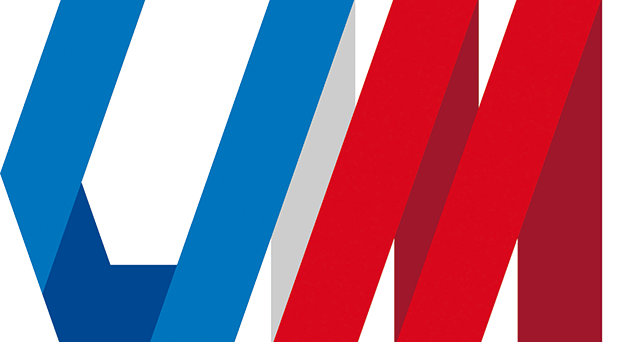
Symbol of fusion "UM" logo mark
In addition to the initials "UBE" and "MITSUBISHI," "UM" also means "YOU & ME" (you and me together) or "YUME (=dreams) & MIRAI (=future)". The "UM" logo mark resembles the shape of the screw, a key part of an injection molding machine that requires precise technology, and is represented in two colors, UBE blue and Mitsubishi red. It is used as the logo for both companies' fusion machines as well as their sales companies.
2018
Fusion Machine No. 1: Development of the medium-sized all-electric injection molding machine "HH Series"
(Clamping force: 350 to 850 tons)
The first fusion machine jointly developed by Ube Machinery and U-MHI Platech.
Combination of technologies of both companies, such as "connected" controller MAC-IX, and DIEPREST, which realizes high-performance molding.
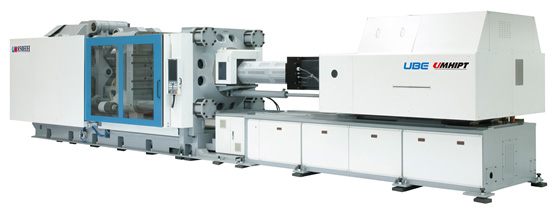
2019
Large-sized 2-platen electric injection molding machine "emⅢ Series" developed
(Clamping force: 1050 to 2000 tons)
Further evolution of the "em II Series" with a lower floor and improved energy-saving performance.
Machine at the pinnacle of 2-platen injection molding machines.
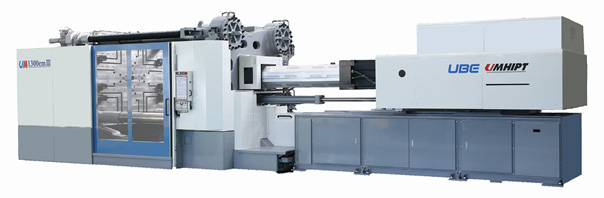
August 1, 2020 Merged U-MHI Platech Co., Ltd. and U&M Plastic Solutions Co., Ltd. and opened Nagoya Machinery Works as a dedicated factory for injection molding machines.
UBE Machinery, Inc. of the U.S. absorbs U-MHI Platech America, Inc., a U.S. service subsidiary of U-MHI PLATECH Co.,Ltd.
2020
August: Nagoya Machinery Works of Ube Machinery Corporation, Ltd. begins operations.
Nagoya Machinery Works starts operation as a state-of-the-art factory dedicated to injection molding machines, equipped with screw processing facilities and producing mainly the mainstay large two-platen electric injection molding machines "emII, emIII Series".
It is located in Aichi Prefecture, Japan, where the manufacturing industry is concentrated.
This is our first production plant in Japan outside of the Ube (in Yamaguchi prefecture) area.
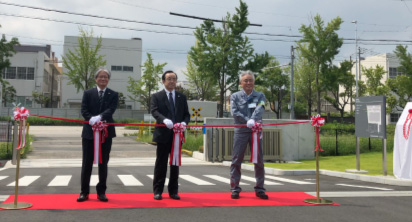
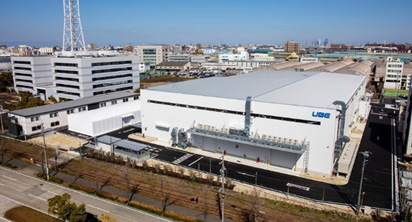
Large-sized toggle type all-electric injection molding machine "1300HH"
Large-sized machine line-up, our strongest point, is added to the "HH Series" of fusion machines.
Realizes the industry's fastest dry cycle and the industry's smallest machine length for toggle type machines.
Large-sized HH Series (Clamping force: 1300, 1360 tons)
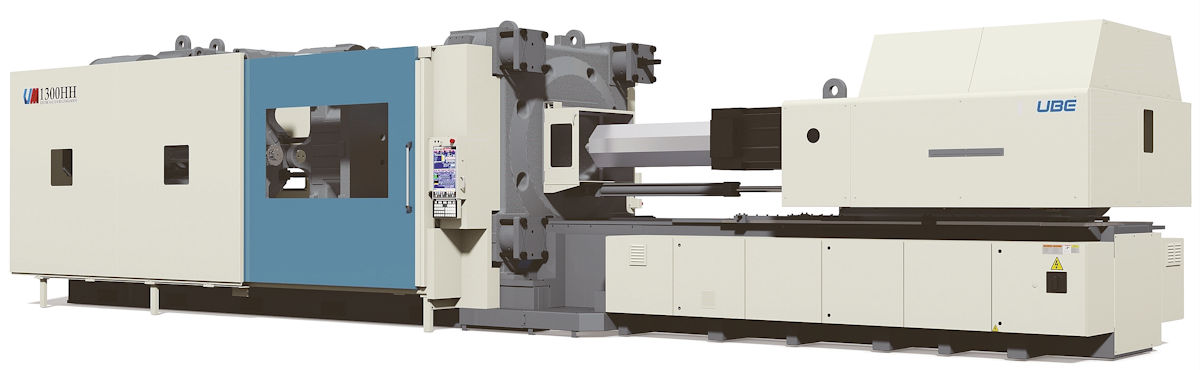
2021
Large-sized 2-Platen Servo-Hydraulic Injection Molding Machine "MMX II Series" developed
Successor to the "MMX Series" mainly targeting overseas markets.
Further technological advancements such as a low-floor design and MAC-IX control system, while maintaining cost competitiveness.
MMX II Series (Clamping force: 1600 tons)
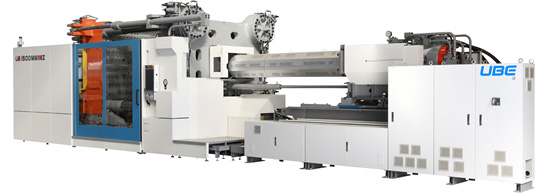